Plastic injection molding is a process of injecting molten plastic into a mold cavity to create a solid object. It is widely used in the manufacturing industry because of its versatility, efficiency, and precision. However, not all injection molding processes are created equal. To ensure the best results, there are several factors that manufacturers need to pay attention to. In this article, we will discuss what to pay attention to when processing plastic injection molding.
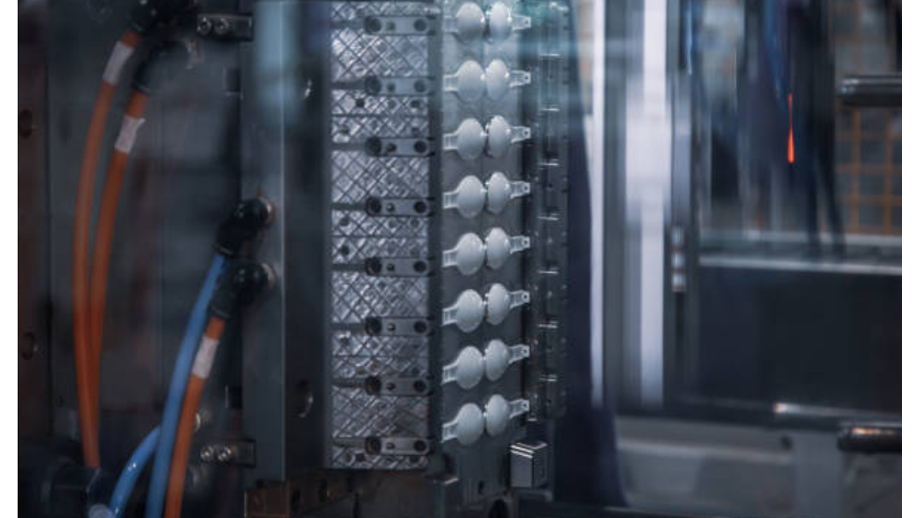
Choosing the Right Material
One of the most important factors in plastic injection molding is choosing the right material. There are many types of plastic available, each with its own unique properties. The material you choose will affect the quality of the final product, as well as the cost and production time. Some common materials used in injection molding include:
Acrylonitrile Butadiene Styrene (ABS): A strong, durable plastic that is resistant to impact and heat.
Polycarbonate (PC): A transparent, lightweight plastic that is resistant to impact and heat.
Polypropylene (PP): A flexible, lightweight plastic that is resistant to chemicals and heat.
Polyethylene (PE): A durable, flexible plastic that is resistant to impact and chemicals.
It is important to choose the right material for your product based on its intended use and the environment it will be used in.
Designing the Mold
The mold design is another important factor in plastic injection molding. The mold needs to be designed to accommodate the material being used and the shape of the final product. It also needs to be designed to allow for easy removal of the product from the mold. The mold design will affect the quality of the final product, as well as the production time and cost. Some important factors to consider when designing the mold include:
The gate type and location: The gate is the point where the molten plastic enters the mold. The gate type and location can affect the quality of the final product and the production time.
The cooling system: The cooling system is important to ensure that the plastic solidifies properly and to prevent warping or shrinkage of the final product.
The ejection system: The ejection system is designed to remove the final product from the mold. It needs to be designed to ensure the product is not damaged during ejection and to prevent the product from getting stuck in the mold.

Controlling the Injection Process
The injection process itself is also critical to the success of plastic injection molding. The process needs to be carefully controlled to ensure that the molten plastic is injected into the mold cavity at the right pressure, temperature, and speed. The injection process will affect the quality of the final product, as well as the production time and cost. Some important factors to consider when controlling the injection process include:
The injection pressure: The injection pressure needs to be high enough to ensure that the molten plastic fills the mold cavity completely, but not so high that it causes the mold to deform or the product to warp.
The injection speed: The injection speed needs to be controlled to ensure that the molten plastic flows smoothly into the mold cavity and to prevent the product from being damaged.
The injection temperature: The injection temperature needs to be controlled to ensure that the molten plastic is at the right consistency and to prevent the product from warping or cracking.
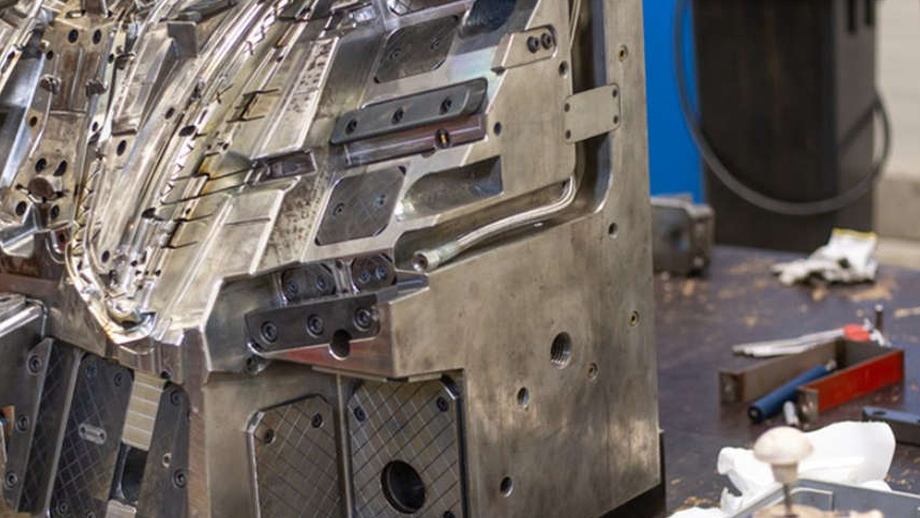
Choosing the Right Manufacturer
Finally, choosing the right manufacturer is also important when processing plastic injection molding. Not all manufacturers are created equal, and the quality of the final product, as well as the production time and cost, will depend on the manufacturer you choose. Some factors to consider when choosing a manufacturer include:
Their experience and expertise in plastic injection molding
Their equipment and facilities
Their quality control processes
Their customer service and support
JS Precision is an excellent injection molding manufacturer with years of experience and a proven track record of success. They have state-of-the-art equipment and facilities, rigorous quality control processes, and a dedicated team of experts who are committed to delivering the best possible results for their customers.
In conclusion, plastic injection molding is a complex process that requires careful attention to detail to ensure success. By choosing the right material, designing the mold properly, controlling the injection process, and choosing the right manufacturer, you can ensure that your plastic injection molding project is a success. Contact JS Precision today to learn more about their services and how they can help you with your plastic injection molding needs.