Injection molding is a widely used manufacturing process for producing plastic products. One of the most common materials used in injection molding is TPE (Thermoplastic Elastomers), which is known for its flexibility, durability, and chemical resistance. However, TPE injection molding can be challenging, and one of the most common issues that manufacturers face is overflow. In this article, we will discuss what to do if there is overflow during TPE injection molding.
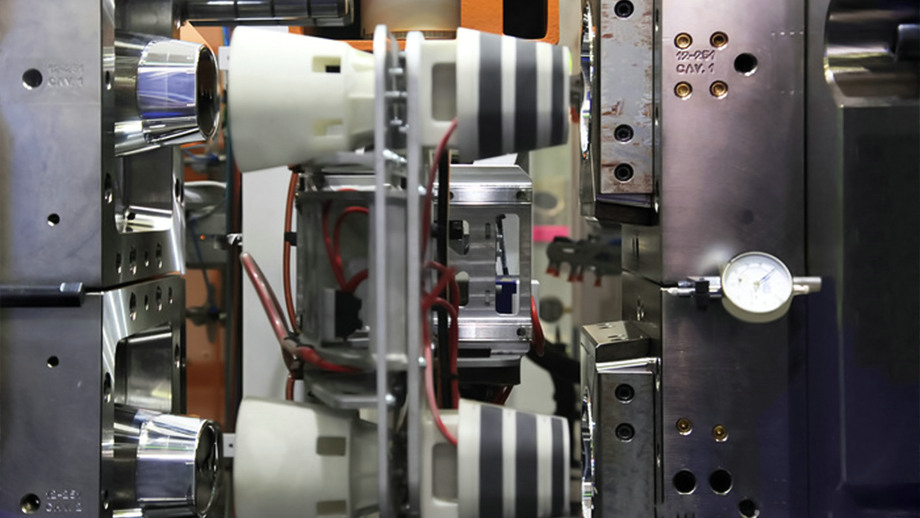
What is Overflow in TPE Injection Molding?
Overflow is a common issue in injection molding, which occurs when the material flows beyond the intended part geometry. Overflow can be caused by various factors, such as incorrect mold design, excessive injection pressure, improper cooling, or insufficient venting. When overflow occurs, it can result in a flash, which is the excess material that is attached to the final product.
How to Prevent Overflow in TPE Injection Molding?
Preventing overflow in TPE injection molding requires careful consideration of several factors, including mold design, injection parameters, and material properties. Here are some tips to help prevent overflow in TPE injection molding:
- Optimize the mold design: The mold design is critical to preventing overflow. The mold should have appropriate venting to allow air to escape during injection and prevent the material from flowing beyond the intended part geometry. The mold should also have a proper gating system to control the flow of material.
- Adjust injection parameters: Injection parameters such as injection pressure, injection speed, and holding pressure can affect the flow of material during injection molding. Adjusting these parameters can help prevent overflow. For example, reducing the injection pressure or injection speed can help prevent the material from flowing beyond the part geometry.
- Use appropriate material: TPE materials have different properties that can affect their flow during injection molding. Using a material with a higher viscosity can help prevent overflow by slowing down the flow of material.
- Ensure proper cooling: Proper cooling is essential to prevent overflow. The cooling time should be sufficient to allow the material to solidify before the mold opens. Insufficient cooling can cause the material to stick to the mold, resulting in overflow.
What to Do if There is Overflow During TPE Injection Molding?
Even with proper preventive measures, overflow can still occur during TPE injection molding. Here are some steps to take if there is overflow:
- Stop the injection molding process: As soon as overflow is detected, stop the injection molding process to prevent further damage.
- Remove the flash: The excess material that is attached to the final product should be removed using a trimming tool. The trimming tool should be sharp enough to remove the flash without damaging the final product.
- Analyze the cause of overflow: Once the flash is removed, the cause of overflow should be analyzed to prevent it from happening again. The mold design, injection parameters, and material properties should be evaluated to identify the root cause of overflow.
- Adjust the injection parameters: If the cause of overflow is related to injection parameters, such as injection pressure or injection speed, they should be adjusted to prevent overflow from occurring again.
- Modify the mold design: If the cause of overflow is related to mold design, such as insufficient venting or improper gating, the mold design should be modified to prevent overflow from occurring again.
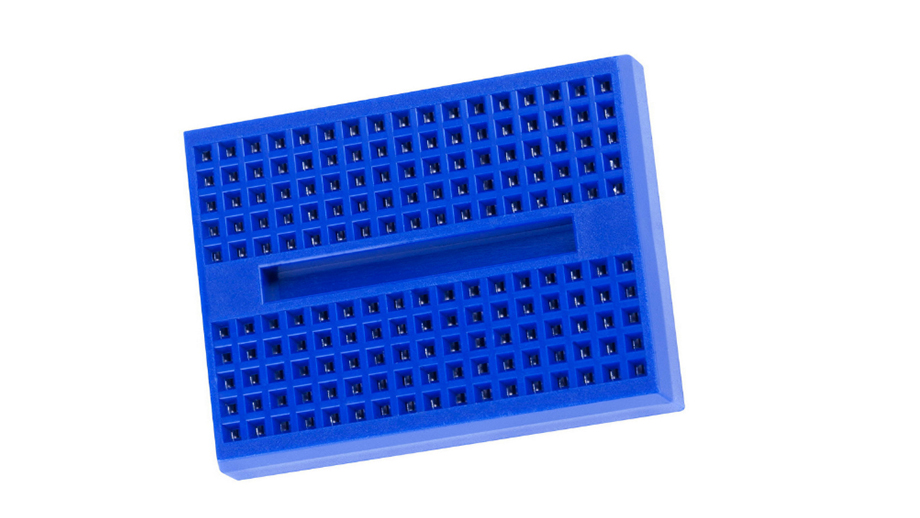
Conclusion
Overflow is a common issue in TPE injection molding, which can result in flash and affect the quality of the final product. Preventing overflow requires careful consideration of mold design, injection parameters, and material properties. If overflow does occur, it is essential to stop the injection molding process, remove the flash, and analyze the cause to prevent it from happening again. At JS Precision, we have years of experience in TPE injection molding and can help you prevent and address overflow issues. Contact us today to learn more about our injection molding services.