What is plastic extrusion used for?
Plastic Extrusion can form almost all thermoplastics and some thermosets.
It is a continuous product, such as tubes, plates, wires, films, wires and cables, etc. Extrusion molding is one of the important methods in plastic molding processing.
It refers to a molding method in which heated and melted plastic is forced to pass through a die under pressure to become a continuous profile with a constant cross-section by means of the extrusion action of a screw or a plunger.
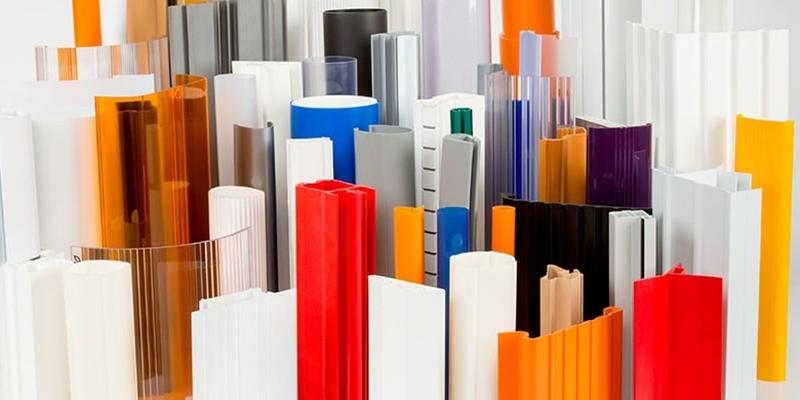
Thermoplastic extrusion in its current form has been around for almost a century, but it is still a powerful tool for the mass production of continuous profile parts. JS precision technology works with Customers to create custom plastic extrudates for parts.
This article presents the basics of plastic extrusion, including what kind of thermoplastic can be extruded, what products plastic extrusion is used to make, and how plastic extrusion compares with aluminum extrusion.
Extruded plastics
Extruded plastics are usually fed into the extruder in the form of plastic particles, similar to those used for injection molding. Other forms include powders, flakes, and pellets.
Common extruded plastics include:
Polyethylene (PE) : extruded between 400°C (low density) and 600°C (high density)
Polystyrene: ~450°C
Nylon: 450°C to 520°C
Polypropylene: ~450°C
PVC: between 350°C and 380°C
Plastic Extrusion Applications
JS precision technology can make a variety of parts, as long as the parts have a consistent profile. Plastic extrusion profiles are ideal for pipes, door profiles, automotive parts and more.
Sheets and Cast Films
The construction industry is one of the major consumers of plastic sheets. These are usually used for glazing on doors, windows, bulletproof sheet, and protective sheet.
Aside from this, sheets can also be used as protective covers over walkways and as sound barriers in commercial and industrial applications. Refrigerator liners, food containers, decorative panels, and lamination applications also utilize plastic sheets.
Cast films, on the other hand, are used in the food, agricultural, and packaging industries. Specifically, cast films are used in:
Food wrapping
Agricultural film for weed control
Protective film during shipments
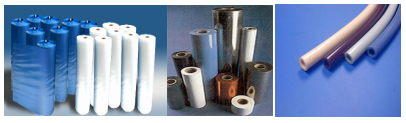
Wire and Cable Coating
Plastic extrusion can be employed to coat wires and cables primarily for insulation and protection. Coating wires and cables are done by a crosshead extrusion process.
For this application, the common polymeric materials used are:
Polyethylene
Polyvinyl chloride
Polyamide
Polybutylene terephthalate
Thermoplastic elastomers
Ethylene propylene copolymers
Polypropylene
Fluoropolymers
Pipe and Tubing
Pipes and tubes are widely used in different industries. Specifically, these plastic extrusion products are utilized as:
Water or sewage pipes
Drinking straws
Vacuum lines
Medical tubing
Plastic pipettes
Circular plastic posts
Refrigeration hose
Other related applications
Door and Window Profiles
Plastic window and door frames are ideal for extrusion because of their continuous profile and length. PVC is a popular material for this plastic extrusion application and all plastic extrusion profiles related to household accessories.
Extrusion Blow Molding
Extrusion blow molding is often employed to create huge, irregularly shaped hollow parts. The automotive industry is a key customer of extrusion blow molding products including parts of bumpers, knee bolsters, air conditioning, side view mirrors, door handles, and so forth.
*Windshield Wipers And Squeegee
Windshield wipers for cars are usually extruded. The extruded plastic can be a synthetic rubber material such as EPDM, or plastic extrusion companies can perform co-extrusion of synthetic rubber with natural rubber. Manual squeegee blades work similarly to windshield wipers.
Blinds
Blinds (curtains) made of many identical slats can be extruded using thermoplastics. The profile is usually short and sometimes rounded on one side. Polystyrene is commonly used in faux wood shutters.
Plastic Extrusion vs Aluminum Extrusion
In addition to thermoplastics, aluminum components with continuous profiles can also be extruded.
Advantages of using aluminum for extruded parts include light weight, electrical conductivity and recyclability. Common aluminum extrusion applications include rods, tubes, wires, pipes, fencing, rails, frames and radiators.
Unlike plastic extrusion, aluminum extrusion can be either hot or cold: hot extrusion is carried out between 350°C and 500°C, cold extrusion at room temperature.
Advantages and disadvantages of plastic extrusion
Plastic extrusion processes offer manufacturers several advantages, including flexibility and versatility. Here are some other advantages offered by plastic extrusion.
Advantages of plastic extrusion
After Extrusion Manipulation: After extrusion and before cooling, it is still easy to change the shape of the hot plastic. This gives the manufacturer a lot of leeway to ensure the quality of the final product is first class.
Relatively cheap: Plastic extrusion is cost effective compared to other processes for developing plastics. The reason is that it does not require sophisticated tools.
Flexibility: Plastic extrusion provides considerable flexibility when the cross sections are consistent. In other words, plastic extruded profiles can produce complex shapes if the cross section is constant.
Disadvantages of plastic extrusion
Size change: Hot plastic expands many times when taken out of the plastic extruder. It can lead to deviations in the original size of the product. In addition, it is difficult to determine how much the size of the thermoplastic will change.
Limited Product: The type of product manufactured using this technology is limited. In addition, making different things requires a significant investment in another type of extrusion equipment.
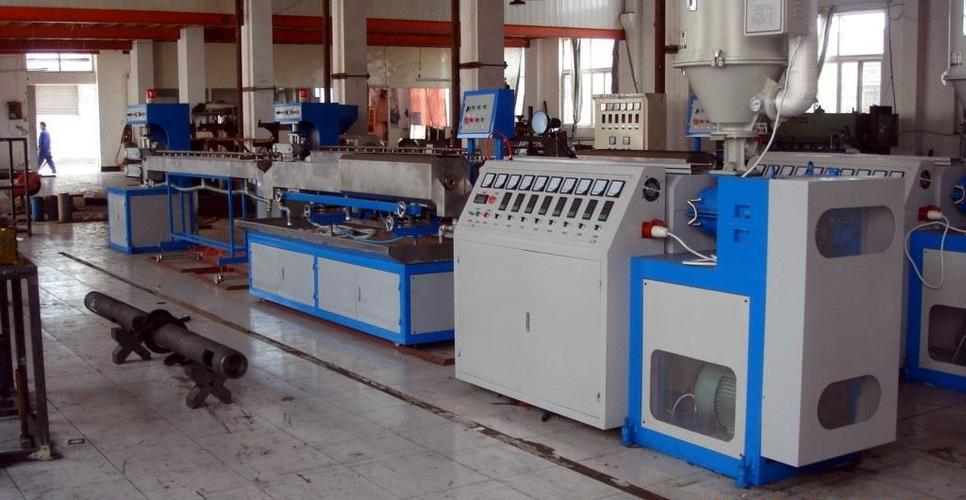
JS precision technology Co.., Ltd is a professional production and processing company of injection molding, extrusion molding, injection molding, plastic coated products, secondary molding and other products, with a complete and scientific quality management system. JS precision technology Co.., Ltd integrity, strength and product quality are recognized by the industry.