Injection molding is one of the most popular manufacturing processes for plastic parts. It involves injecting molten plastic into a mold cavity, where it cools and solidifies into the desired shape. This process is used to create a wide range of products, from toys and containers to automotive parts and medical devices. However, injection molding is a complex process that requires careful attention to detail at every stage. In this article, we will explore the important stages in the injection molding process of plastic parts.
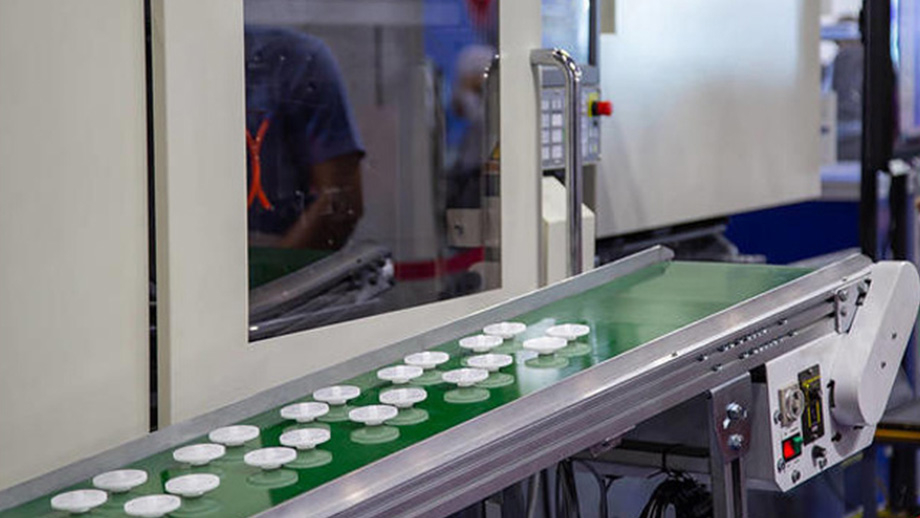
- Design
The first stage in the injection molding process is design. This involves creating a 3D CAD model of the part that is to be produced. The design stage is critical because it determines the shape, size, and functionality of the part. The design must also take into account factors such as material selection, part orientation, and the location of injection points.
- Tooling
Once the design has been finalized, the next stage is tooling. Tooling involves creating the mold that will be used to produce the part. The mold is typically made from steel or aluminum and is designed to withstand high pressure and temperature. The tooling process can take several weeks or months to complete, depending on the complexity of the part.
- Material Selection
After the mold has been created, the next stage is material selection. The choice of material will depend on the requirements of the part, such as strength, durability, flexibility, and heat resistance. Common materials used in injection molding include polypropylene, polystyrene, and polyethylene.
- Injection Molding
The injection molding stage is where the actual production of the part takes place. Molten plastic is injected into the mold cavity under high pressure and temperature. The plastic fills the cavity and takes on the shape of the mold. After a few seconds, the plastic cools and solidifies, and the mold is opened to release the finished part.
- Cooling
After the part has been molded, it needs to be cooled before it can be handled. Cooling can be done using air or water cooling. The cooling time will depend on the size and complexity of the part.
- Ejection
Once the part has been cooled, it is ejected from the mold. Ejection can be done manually or with the use of an ejector pin. The part is then inspected for any defects or imperfections.
- Finishing
The final stage in the injection molding process is finishing. This involves removing any excess material, such as flash or burrs, and adding any necessary features, such as threads or logos. Finishing can be done using various techniques, such as trimming, sanding, or polishing.

In conclusion, the injection molding process is a complex and multi-stage process that requires careful attention to detail. From design and tooling to material selection and finishing, each stage of the process plays a critical role in producing high-quality plastic parts. By understanding the important stages in the injection molding process, customers can make informed decisions about their manufacturing needs. If you have any questions or would like to learn more about injection molding, please contact us at JS Precision.