If you’re in the manufacturing industry, you know the importance of precision when it comes to injection molding. Injection molding is a process that involves melting plastic pellets and injecting them into a mold. The melted plastic takes the shape of the mold and then cools and solidifies to form the final product. However, sometimes the finished product doesn’t turn out as expected. One of the most common issues with injection molding is uneven shrinkage. In this article, we’ll explore the reasons for uneven shrinkage and how to avoid it.
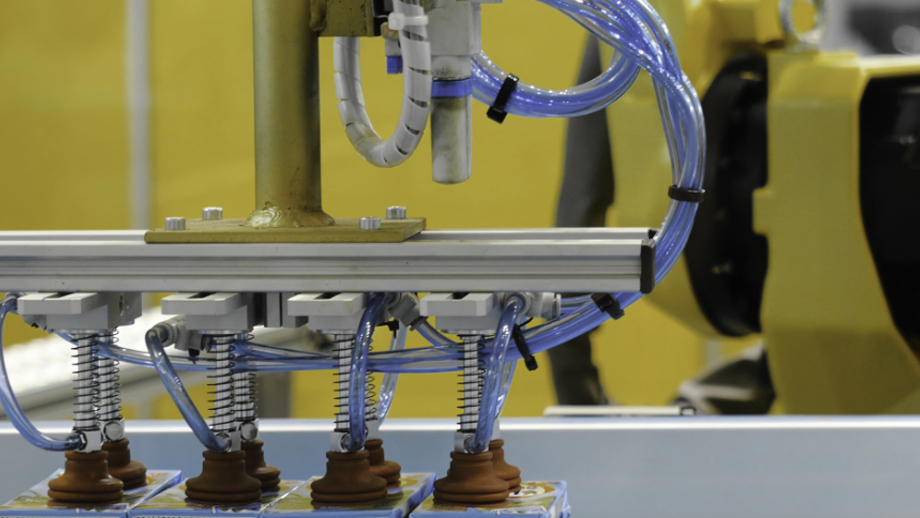
What is Shrinkage?
Before we dive into uneven shrinkage, it’s important to understand what shrinkage is. Shrinkage is the reduction in size of the molded part compared to the size of the mold. This is caused by the cooling and solidifying of the plastic. The amount of shrinkage can vary depending on the plastic material used and the design of the mold. It’s important to take shrinkage into account when designing the mold to ensure the final product is the correct size.
Reasons for Uneven Shrinkage
- Material Selection: The plastic material used in injection molding can have a significant impact on shrinkage. Different materials have different shrinkage rates, and some materials are more prone to uneven shrinkage than others. It’s important to select the right material for the product being manufactured.
- Mold Design: The design of the mold can also impact shrinkage. If the mold isn’t designed correctly, it can cause uneven cooling and result in uneven shrinkage. It’s important to work with an experienced mold designer who can ensure the mold is designed correctly.
- Processing Conditions: The processing conditions used during injection molding can also impact shrinkage. Factors such as temperature, pressure, and cooling time can all affect shrinkage. It’s important to carefully control these processing conditions to ensure consistent shrinkage.
- Part Thickness: The thickness of the molded part can also impact shrinkage. Thicker parts are more prone to uneven shrinkage because they cool at a slower rate than thinner parts. It’s important to design the part with the correct thickness to ensure consistent shrinkage.
How to Avoid Uneven Shrinkage
- Material Selection: Choose a plastic material with a low shrinkage rate and that is less prone to uneven shrinkage.
- Mold Design: Work with an experienced mold designer to ensure the mold is designed correctly and allows for even cooling.
- Processing Conditions: Carefully control the processing conditions to ensure consistent shrinkage. Use sensors and other monitoring tools to ensure the processing conditions remain consistent throughout the injection molding process.
- Part Thickness: Design the part with the correct thickness to ensure consistent shrinkage. Consider adding ribs or other features to thicker parts to help them cool more evenly.
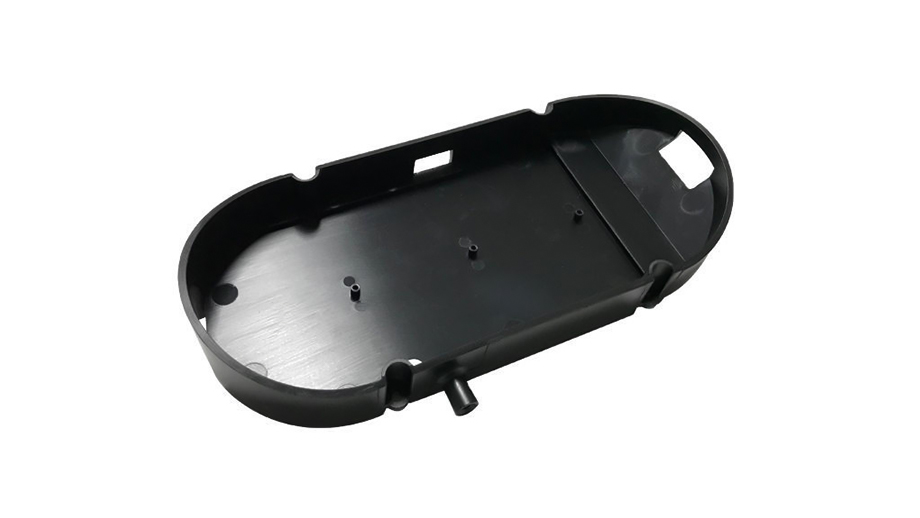
Conclusion
Uneven shrinkage is a common issue in injection molding, but it can be avoided with the right materials, mold design, processing conditions, and part thickness. If you’re experiencing issues with uneven shrinkage, it’s important to work with an experienced injection molding manufacturer like JS Precision. With years of experience and a commitment to quality, JS Precision can help ensure your injection molded parts are always precise and consistent. Contact us today to learn more.