Manufacturing processes have come a long way over the years, and computer numerical control (CNC) machines have played a significant role in revolutionizing the industry. These machines have provided manufacturers with greater precision and efficiency than ever before, making it easier to produce high-quality parts and products quickly. However, even with the most advanced technology, quality control remains a crucial factor in ensuring that the final product meets required specifications.
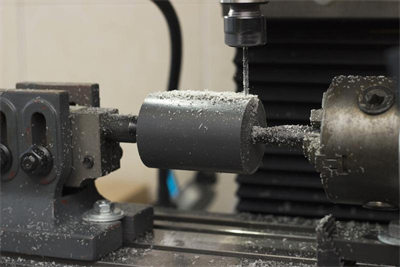
The Role of Quality Control in CNC Processing Parts
CNC machines are programmed to perform specific tasks with high accuracy, but the quality of the final product depends on several factors that can affect the manufacturing process. These factors include the quality of the raw materials, the accuracy of the machine’s programming, and the skill of the operator. Quality control plays a critical role in identifying and addressing any issues that may arise during the manufacturing process. By monitoring the process and inspecting the final product, quality control can ensure that the CNC machine produces parts that meet required standards.
Quality control is particularly important in CNC processing parts because of the precision required in this type of manufacturing. Even minor issues with the raw materials or the programming can lead to significant defects in the final product, which can be costly to fix or can lead to customer dissatisfaction. By implementing quality control measures, manufacturers can catch these issues early on and address them quickly, reducing the risk of defects and errors in the final product.
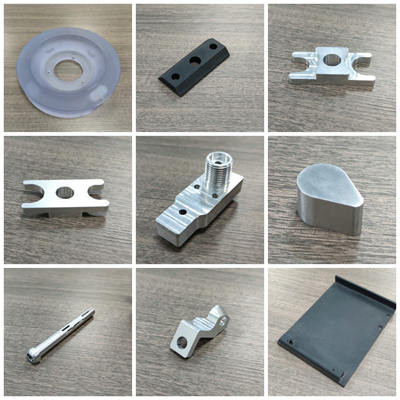
Benefits of Quality Control in CNC Processing Parts
Implementing quality control in CNC processing parts has several benefits. First, it helps to identify and correct any issues that may arise during the manufacturing process, reducing the risk of defects or errors in the final product. This, in turn, can save manufacturers time and money in the long run by reducing the need for rework or scrap. Second, quality control can improve the efficiency of the manufacturing process by ensuring that the machine is operating at its optimal level. Finally, quality control can improve customer satisfaction by ensuring that the final product meets required specifications.
Another benefit of quality control is that it can provide manufacturers with valuable data that can be used to improve the manufacturing process further. By analyzing the data collected during quality control inspections, manufacturers can identify areas of the process that could be improved, leading to even greater efficiency and accuracy in CNC processing parts.
The Future of Quality Control in CNC Processing Parts
As technology continues to advance, the role of quality control in CNC processing parts is likely to become even more critical. New tools and techniques, such as artificial intelligence and machine learning, may allow for more precise monitoring and analysis of the manufacturing process. These advances could lead to even greater efficiency and accuracy in CNC processing parts.
Conclusion
In summary, quality control is a crucial factor in ensuring that CNC processing parts meet required specifications. By monitoring the manufacturing process and inspecting the final product, quality control can help to identify and correct any issues that may arise. Implementing quality control in CNC processing parts has several benefits, including improved efficiency, reduced risk of defects, and improved customer satisfaction. As technology continues to advance, the role of quality control in CNC processing parts is likely to become even more critical, providing manufacturers with even greater opportunities to produce high-quality parts and products.