Our Surface Finishing Services
JS Precision Technology offers a wide variety of surface finishing services. For Example Deburr, Smooth finish, Painting, Brushing, Polishing, Silk-screen, Sandblasting, Anodizing, E-coating, Powder Coating, Plating and Logo Printing, etc.
We usually do hand work after parts are machined, painting is the most common finishing we can do in-house.
Surface Finishing : Bead blasted/Sandblasted
Bead blasting or Sandblasting can effectively remove machined marks. Create a better finish for the parts. We currently have two kinds of grit, steel and glass grit. Steel grit is used for steel parts, while glass grit is used for aluminum parts. Our default grit size is #110.
Brushing
When the parts are completed and deburred. The parts will be sent to the bushing machine. After the surface is finished, it will show a vertical stripe texture, which will also increase the gloss of the parts. The brushing is suitable for cosmetic parts, not for corrosion resistance purposes. Brushing is suitable for a flat surface, not for irregular surface.
As machined
This is the standard finish of LS. When the parts are completed, the burrs will be removed. The machining marks and light scratches are visible. The roughness is Ra 3.2μm / Ra 126μin. This apply to metal parts and plastic parts.
Smooth Machining
A smooth machining surface is one in which the parts are processed slower than in the “As machined” version. It can have a better surface roughness, but the machined marks are still visible. The standard smooth surface roughness is Ra 1.6 μm (64 μin).
Fine machining
Fine machining means when the parts are completed slower than “smooth machining”. It can have a better surface roughness, but the machined marks are still slightly visible. The standard surface roughness is Ra 0.8μm/Ra 32μin.
Polishing
When parts are completed, we will manually polish the parts on multiple sides. The machined marks are not visible. The roughness is Ra 0.8μm / Ra 32μm.
Vapor Polish
This process is only used for parts made of PC materials. When the parts are finished, the burrs will be removed and the parts will be vapor polished. The part will achieve an optically transparent state. This surface treatment is suitable for purposes where transparency of the part is required.
Zinc Plating
Zinc plating refers to the surface of the metal parts, alloy, or other materials coated with a layer of zinc to play a beautiful, rust prevention and other surface treatment technology. It is usually done after the parts are completed machining and after the burrs are removed. Common colors for zinc plating are black, blue, and full color.
Black Oxide
Black oxide is used in steel parts to prevent rust and corrosion. Because the steel is different, the black degree of the parts after the completion of the oxidation blackening process is different, there are deep and light. Machining marks are clearly visible.
Electroless nicel plating
The parts are completed, and the deburrs will be removed before electroless plating. The color is clear, and the machined marks are still visible. Electroless nickel plating will increase the corrosion resistance and wear resistance of the parts.
Passivation
The parts are completed, and the deburrs will be removed before passivation. Passivation will improve the corrosion resistance and increase the life time of the parts.
Chromate conversion coating
Chromate conversion is a layer of film to protect the parts from corrosion and maintain the conductive properties of the parts. The parts are completed, and the deburrs will be removed before chromate conversion. The color is clear, and the machined marks are still visible.
Gloss effect
It is currently available in four gloss effects including no gloss, matte, semi-matte, and high glossy.
The thickness of the film
with a film thickness of 60-80mm, among which our default effect is matte and semi-glossy.
Harden/Heat Treatment
Hardening refers to the process of hardening the surface of the part by appropriate methods while the core of the part still has strength and toughness. Through this treatment, the wear resistance and fatigue resistance of the parts can be improved, and because the heart of the parts still has good toughness and strength, so it has good resistance to impact load. The commonly used surface hardening treatment methods mainly include Carburizing, nitriding, quenching, etc.
Pad printing/Silk screen printing
Parts can be silkscreened in specific areas after they are finished, with your logo or some specific symbols. When parts need to be silkscreened you need to provide a vector image used by the silkscreen process, it is usually in AI or PDF format. This one is usually used for the purpose of personalizing your parts.
Hanging traces
Powder coating is mainly used to protect parts from corrosion and get a beautiful appearance of parts. But it is worth mentioning that the parts will be hung by hanging tools in the process of powder coating, and the parts will be covered by hanging tools without powder spraying, so the parts will leave hanging traces which is inevitable. However, the hanger may be suspended inside the part or suspended on a non-cosmetic surface.
Engraving/Etch
Parts can be engraved/etched in specific areas after they are finished, with your logo or some specific symbols. This one is usually used for the purpose of personalizing your parts.
Gold plating
Gold plating is done after the parts are finished machining and the burrs are removed. The machined traces are still visible. The purpose of gold plating is generally used for cosmetic parts.
Powder coating
When the parts are completed and deburred. There will be a layer of powder The powder coating applies to all metal parts. The parts will be sprayed with a layer of powder through the process of powder spraying.
The default texture of powder spraying is flat.
Hanging traces
Powder coating is mainly used to protect parts from corrosion and get a beautiful appearance of parts. But it is worth mentioning that the parts will be hung by hanging tools in the process of powder coating, and the parts will be covered by hanging tools without powder spraying, so the parts will leave hanging traces which is inevitable. However, the hanger may be suspended inside the part or suspended on a non-cosmetic surface.
Tolerance
The tolerances are applied before powder coating.
Anodize Type II
Gloss effect
It is currently available in two gloss effects including matte and glossy.
The thickness of the film
with a film thickness of 0.00007” to 0.0010”, among which our default effect is matte and semi-glossy.
Hanging traces
Anodizing is mainly used to protect parts from corrosion and get a beautiful appearance of parts. But it is worth mentioning that the parts will be hung by hanging tools in the process of powder coating, and the parts will be covered by hanging tools without powder spraying, so the parts will leave hanging traces which is inevitable. However, the hanger may be suspended inside the part or suspended on a non-cosmetic surface.
Tolerance
The tolerances are applied before powder coating.
Let's build something great, together
Contact us for rapid and efficient machining services. Leave us a message now for swift and effective completion of your project
Anodizing type II
All tolerances apply after anodizing.
Anodizing type III
All tolerances apply after anodizing.
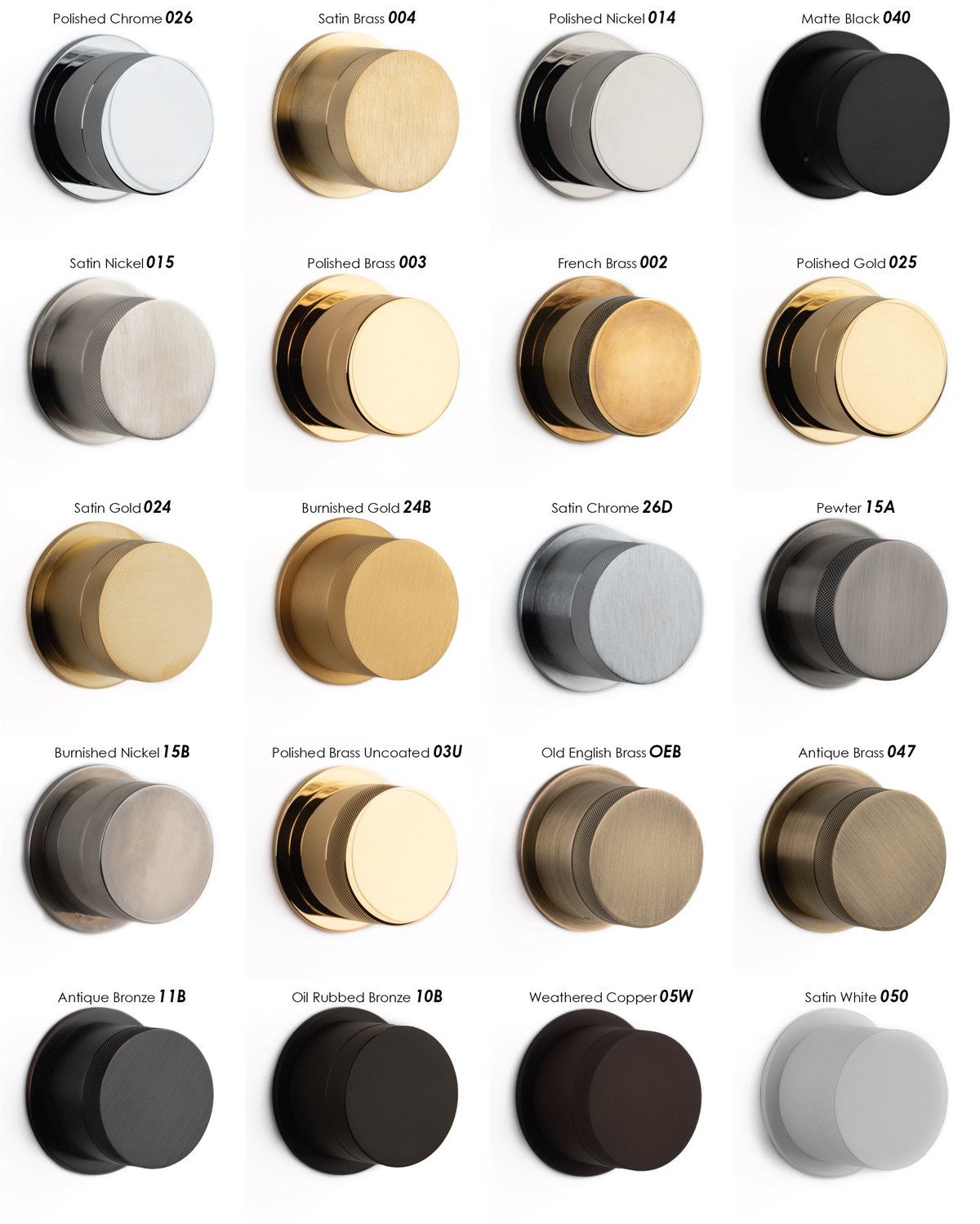
Surface Finishing Services Custom Parts Online Quote Manufacturer
Start Your Project With A Free Quote