Injection molding is a widely used manufacturing process that involves injecting molten material into a mold cavity. While it is a highly efficient process, it can also lead to stress problems in the final product. Stress is a force that can cause deformation or even failure of the product over time. To avoid this, it is important to adjust the injection molding process parameters. In this article, we will discuss the key parameters that need to be adjusted to solve stress problems in injection molding.
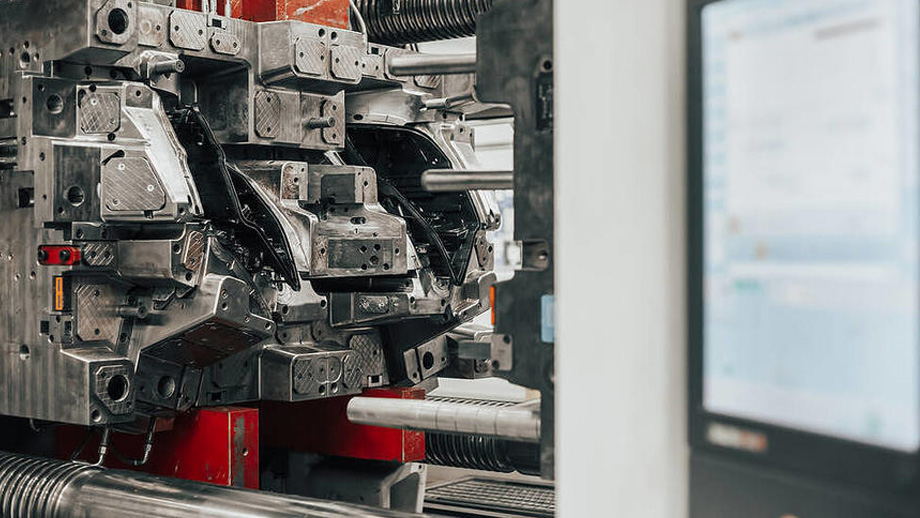
- Injection Speed
The injection speed is the rate at which the molten material is injected into the mold cavity. If the injection speed is too high, it can cause shear stress in the material, which can lead to stress problems in the final product. On the other hand, if the injection speed is too low, it can cause flow marks or sink marks on the surface of the product. Therefore, it is important to adjust the injection speed to a level that balances these factors.
- Injection Pressure
The injection pressure is the force that is applied to the molten material to push it into the mold cavity. If the injection pressure is too high, it can cause excessive stress in the material, which can lead to deformation or failure of the product over time. On the other hand, if the injection pressure is too low, it can cause incomplete filling of the mold cavity or other defects in the final product. Therefore, it is important to adjust the injection pressure to a level that ensures complete filling of the mold cavity without causing excessive stress in the material.
- Cooling Time
The cooling time is the time that is allowed for the molten material to solidify inside the mold cavity. If the cooling time is too short, it can cause warpage or other stress problems in the final product. On the other hand, if the cooling time is too long, it can increase the cycle time and reduce the productivity of the injection molding process. Therefore, it is important to adjust the cooling time to a level that ensures proper solidification of the material without increasing the cycle time.
- Mold Temperature
The mold temperature is the temperature of the mold cavity during the injection molding process. If the mold temperature is too high, it can cause the material to stick to the mold cavity, which can lead to stress problems in the final product. On the other hand, if the mold temperature is too low, it can cause incomplete filling of the mold cavity or other defects in the final product. Therefore, it is important to adjust the mold temperature to a level that ensures proper filling of the mold cavity without causing excessive stress in the material.
Conclusion
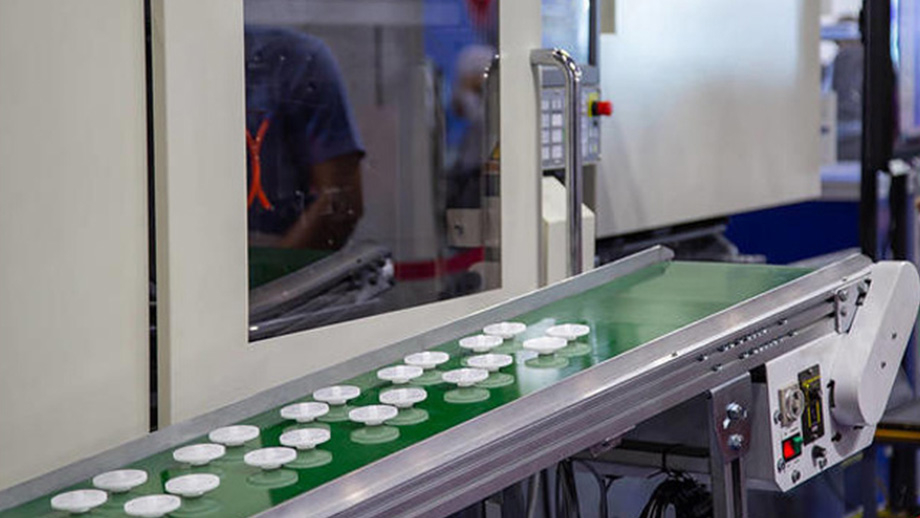
In summary, adjusting the injection molding process parameters is crucial to solving stress problems in the final product. The key parameters that need to be adjusted include injection speed, injection pressure, cooling time, and mold temperature. By optimizing these parameters, it is possible to achieve high-quality injection-molded products that are free from stress and deformation. JS Precision, a leading injection molding manufacturer, has extensive experience in optimizing these parameters to deliver high-quality products to its customers. Contact us today to learn more about our injection molding services.