Injection molding is a popular manufacturing process used to create a wide range of products, from toys to automotive parts. However, it’s not without its challenges. Flashing, overflowing, and warping are common issues that can arise during the injection molding process, leading to wasted materials and increased costs. In this article, we’ll take a closer look at these problems and explore some solutions to help you achieve high-quality injection molded products.
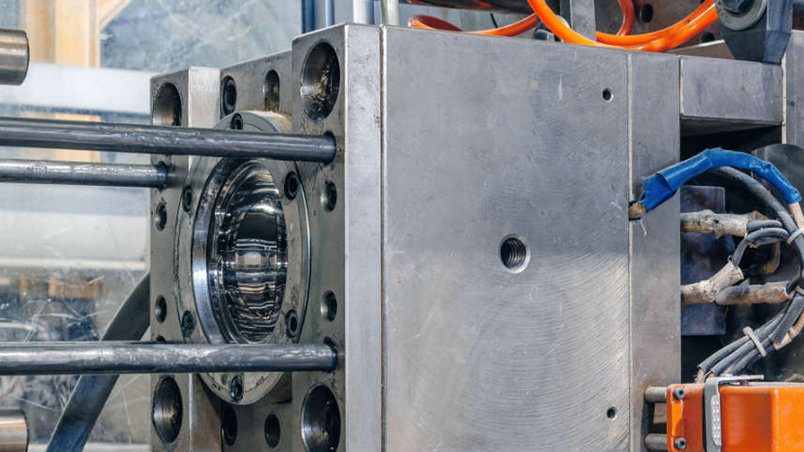
What is Flashing?
Flashing is excess material that protrudes from the parting line of an injection molded product. It’s caused by the plastic seeping between the mold’s two halves, resulting in an undesirable finish and, in some cases, reducing the part’s functionality. Flashing can also lead to increased labor costs, as workers must manually remove the excess material.
The following are some common solutions to prevent flashing:
- Increase the clamping force: Insufficient clamp force can cause the mold to separate slightly, allowing the plastic to seep between the two halves. Increasing the clamping force can prevent this problem from occurring.
- Reduce the injection speed: High injection speeds can cause the plastic to move too quickly, leading to flashing. Reducing the injection speed can help to alleviate this problem.
- Adjust the gate size and location: The gate is where the plastic enters the mold. If the gate is too large or in the wrong location, it can cause flashing. Adjusting the gate size and location can help to prevent this issue.
What is Overflowing?
Overflowing is when the plastic spills out of the mold cavity, resulting in an irregular shape and poor-quality finish. This issue is often caused by too much plastic being injected into the mold, or by the mold being too hot. Here are some solutions to prevent overflowing:
- Reduce the injection pressure: High injection pressure can cause too much plastic to be injected into the mold, resulting in overflowing. Reducing the injection pressure can help to alleviate this issue.
- Increase the cooling time: If the mold is too hot, the plastic may not solidify properly, causing it to overflow. Increasing the cooling time can help to prevent this problem.
- Adjust the venting system: The venting system allows excess air to escape from the mold. If the venting system is not working correctly, it can cause overflowing. Adjusting the venting system can help to prevent this issue.
What is Warping?
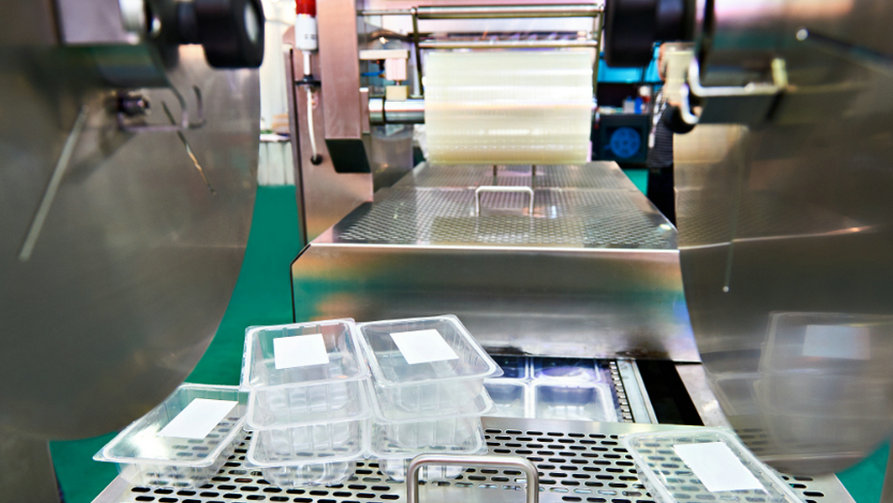
Warping is when an injection molded product becomes distorted or deformed after it’s removed from the mold. This problem is often caused by uneven cooling, which can lead to internal stress and deformation. Here are some solutions to prevent warping:
- Increase the cooling time: If the product cools too quickly, it can cause uneven cooling, leading to warping. Increasing the cooling time can help to prevent this problem.
- Adjust the mold temperature: If the mold temperature is too high or too low, it can cause warping. Adjusting the mold temperature can help to prevent this issue.
- Use a shrinkage compensator: A shrinkage compensator is a tool that can be used to predict and compensate for the shrinkage that occurs during the cooling process. Using a shrinkage compensator can help to prevent warping.
Conclusion
In conclusion, flashing, overflowing, and warping are common issues that can arise during the injection molding process. However, with the right solutions, you can prevent these problems and achieve high-quality injection molded products. At JS Precision, we offer a range of injection molding services to help you create the products you need. Contact us today to learn more about our services and how we can help you with your injection molding needs.