Are you looking to improve the dimensional accuracy of your injection molded parts? Look no further than adjusting your process parameters. In this article, we will explore the various process parameters that can be adjusted to achieve improved dimensional accuracy in your injection molded parts.
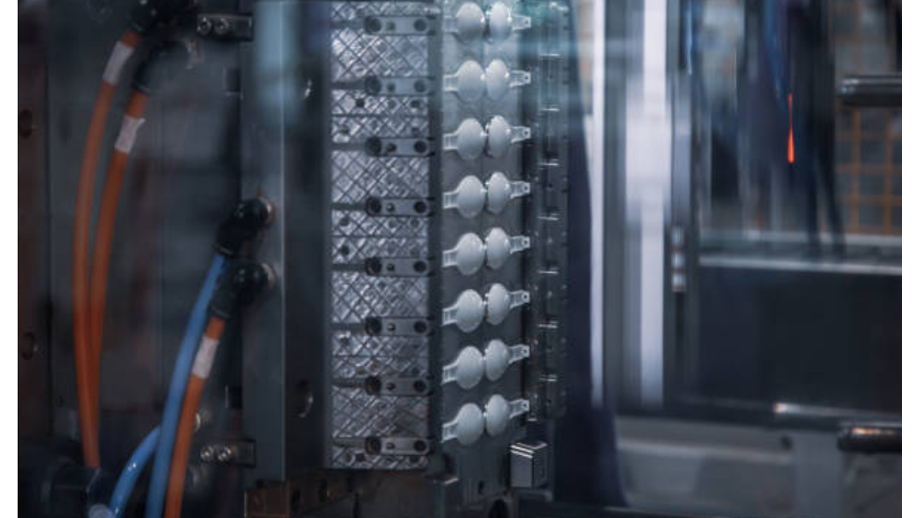
Introduction
Injection molding is a widely used manufacturing process that produces a wide range of plastic products. However, one of the biggest challenges in injection molding is achieving the desired dimensional accuracy for the parts being produced. Dimensional accuracy is crucial for ensuring that the parts fit and function properly in their intended applications.
Several important parameters
Fortunately, there are several process parameters that can be adjusted to improve dimensional accuracy. Let’s explore these parameters in more detail.
Injection Speed
Injection speed is a critical parameter that affects the filling and packing stages of the injection molding process. A higher injection speed can improve the dimensional accuracy of the part by reducing the chances of voids or sink marks. However, it is essential to ensure that the injection speed is not too high, as this can cause flash or over-packing.
Injection Pressure
Injection pressure is another critical parameter that affects the filling and packing stages of the injection molding process. A higher injection pressure can improve the dimensional accuracy of the part by ensuring that the mold cavity is filled completely. However, it is essential to ensure that the injection pressure is not too high, as this can cause flash or over-packing.
Injection Temperature
Injection temperature is a critical parameter that affects the flow behavior of the plastic material. A higher injection temperature can improve the dimensional accuracy of the part by reducing the chances of flow marks or weld lines. However, it is essential to ensure that the injection temperature is not too high, as this can cause degradation or burning of the plastic material.
Mold Temperature
Mold temperature is a critical parameter that affects the cooling and solidification stages of the injection molding process. A higher mold temperature can improve the dimensional accuracy of the part by reducing the chances of warpage or shrinkage. However, it is essential to ensure that the mold temperature is not too high, as this can cause longer cycle times and reduced productivity.
Cooling Time
Cooling time is a critical parameter that affects the cooling and solidification stages of the injection molding process. A longer cooling time can improve the dimensional accuracy of the part by ensuring that the plastic material is fully solidified before the mold is opened. However, it is essential to ensure that the cooling time is not too long, as this can cause longer cycle times and reduced productivity.

Conclusion
In conclusion, adjusting the process parameters of injection molding can significantly improve the dimensional accuracy of injection molded parts. By adjusting the injection speed, injection pressure, injection temperature, mold temperature, and cooling time, manufacturers can achieve the desired dimensional accuracy for their parts. For more information on injection molding and process parameter adjustments, contact JS Precision today.