What is precision plastic injection molding?
Precision plastic injection molding is a manufacturing process that involves producing high-precision and complex parts with tight tolerances and intricate geometries. This guide will provide an in-depth overview of precision plastic injection molding, including the process, benefits, applications, design, materials, equipment, and quality control.
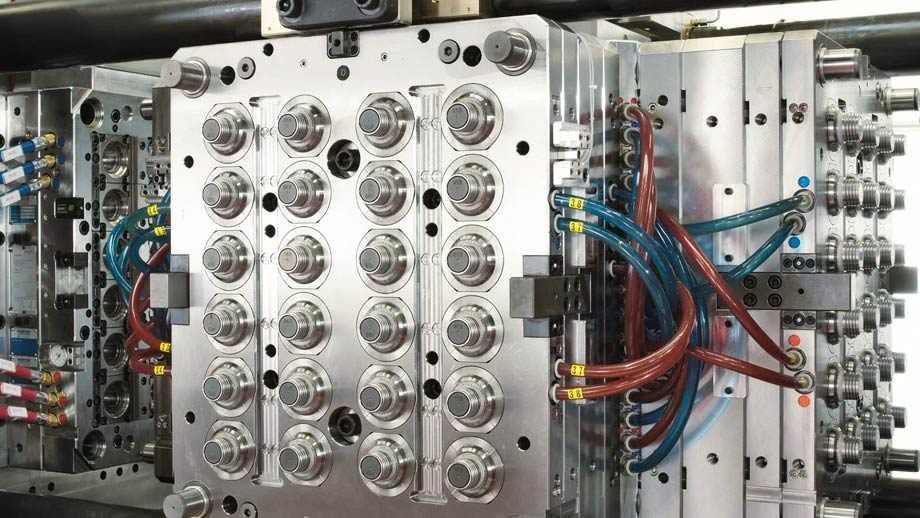
Process of Precision Plastic Injection Molding
It involves several steps, including:
- Designing the mold: The first step in precision injection molding is designing the mold. This involves using computer-aided design (CAD) software to create a 3D model of the part, which is then used to create the mold.
- Creating the mold: Once the mold design is complete, it is created using advanced machinery such as CNC machines, EDM machines, and wire-cut machines. The mold is typically made of steel or aluminum.
- Preparing the material: The plastic material is then prepared by melting it down and adding any required additives, such as colorants or stabilizers.
- Injecting the material: The molten plastic material is then injected into the mold cavity using a high-pressure injection molding machine. The material is injected at a high speed and pressure to ensure that it fills the mold completely.
- Cooling and solidification: Once the mold cavity is filled with the plastic material, the mold is cooled using a cooling system. This helps to solidify the plastic material and ensure that the part maintains its shape.
- Ejecting the part: Once the plastic material has solidified, the mold is opened and the part is ejected using an ejection system. The part is then inspected for quality and any necessary finishing processes are carried out.
Overall, it is a highly advanced and sophisticated process that requires careful planning and execution to ensure that high-quality parts are produced consistently.
Benefits of Precision Plastic Injection Molding
It offers several benefits, including:
- High accuracy and consistency: Precision injection molding allows for the production of parts with high accuracy and consistency, ensuring that each part meets the required specifications.
- Cost-effective: Precision injection molding is a cost-effective method of producing high-quality plastic parts, as it allows for the production of large volumes of parts with minimal waste.
- Wide range of materials: Precision injection molding can be used with a wide range of plastic materials, including thermoplastics, thermosets, and elastomers, allowing for the production of parts with varying properties and characteristics.
- Complex geometries: Precision injection molding can produce parts with complex geometries and features, including thin walls, undercuts, and internal threads.
- Reduced assembly time: Precision injection molding can produce parts with multiple features and components, reducing the need for assembly and reducing the overall production time.
- Improved surface finish: Precision injection molding can produce parts with a smooth and consistent surface finish, reducing the need for additional finishing processes.
Overall, it offers a range of benefits that make it a popular choice for the production of high-quality plastic parts in a wide range of industries.
How Precision plastic injection molding Differs From Traditional injection molding
It differs from traditional injection molding in the following ways:
- Tolerance: Precision plastic injection molding requires tighter tolerances than traditional injection molding. This means that the dimensions of the final product must be more precise, and the variation from the design specifications must be minimal.
- Material selection: it requires the use of high-quality materials that have consistent properties. Traditional injection molding can use a wider range of materials, including recycled materials, which may have more variable properties.
- Mold design and maintenance: The mold used in precision plastic injection molding must be designed and maintained to meet the required specifications. This includes ensuring that the mold is properly cooled and that the mold cavity is free from any defects. Traditional injection molding may be less precise in mold design and maintenance.
- Process control: it requires careful control of the injection molding process to ensure that the plastic material is melted and injected into the mold at the correct temperature and pressure. This includes monitoring the injection speed, holding pressure, and cooling time. Traditional injection molding may have less precise process control.
- Cost: it is typically more expensive than traditional injection molding due to the higher quality materials and tighter tolerances required.
Overall, precision plastic injection molding is a more precise and controlled process than traditional injection molding and is used when higher quality and tighter tolerances are required.
Applications
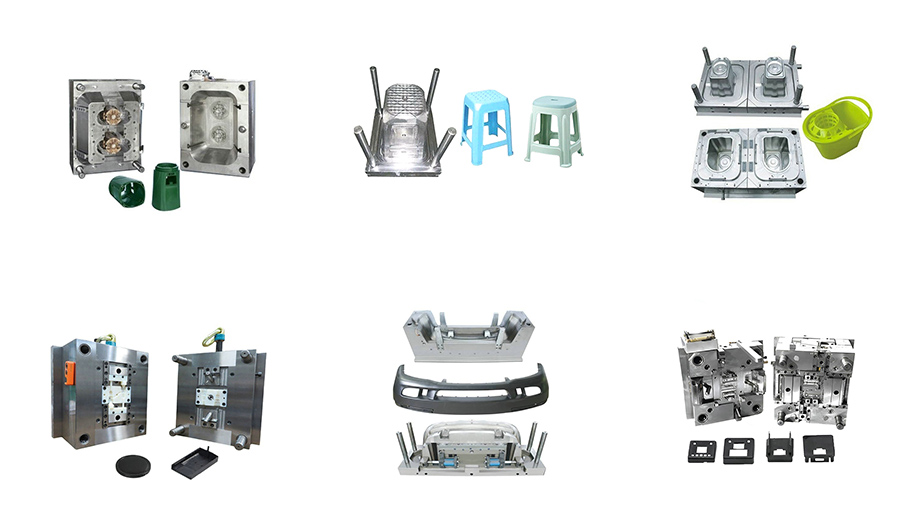
It has a wide range of applications in various industries, including:
- Automotive industry: Precision plastic injection molding is used to produce various automotive parts, such as dashboards, door panels, and interior trims.
- Medical industry: It is used to produce medical devices, such as syringes, vials, and surgical instruments.
- Electronics industry: It is used to produce electronic components, such as connectors, housings, and switches.
- Consumer goods industry: It is used to produce consumer goods, such as toys, kitchen appliances, and household items.
- Aerospace industry: It is used to produce aerospace components, such as aircraft interiors, ventilation systems, and cockpit controls.
Overall, precision plastic injection molding is a versatile manufacturing process that can be used to produce high-quality parts for a wide range of industries and applications.
Designing
Designing for precision plastic injection molding involves several considerations to ensure that the final product is of high quality and meets the required specifications. Some of the key considerations include:
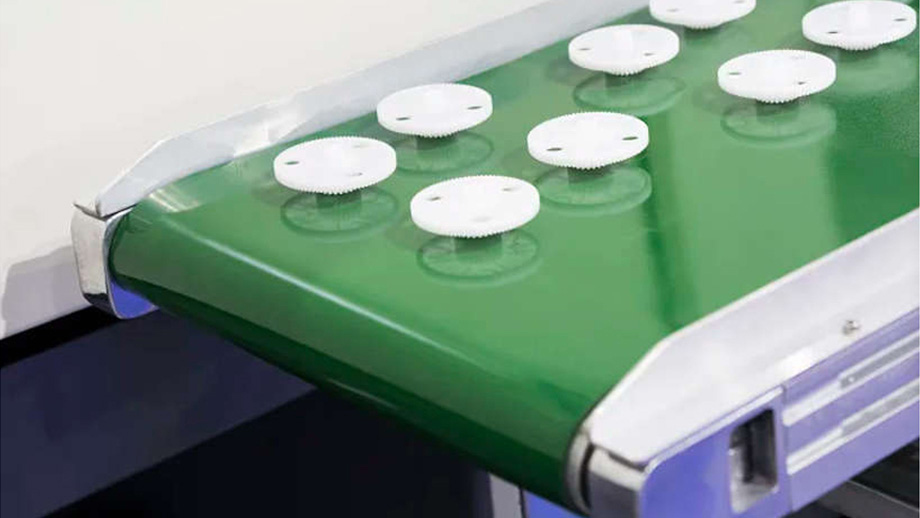
- Wall thickness: The design should have a uniform wall thickness to ensure that the plastic material flows evenly during the injection molding process. Uneven wall thickness can cause defects such as warping, sink marks, and voids.
- Draft angles: The design should have draft angles to allow for easy ejection of the part from the mold. Draft angles also help to reduce the risk of damage to the part during ejection.
- Gate location: The gate location should be carefully chosen to ensure that the plastic material flows evenly throughout the mold cavity. The gate should also be located in an area that allows for easy removal of the gate mark.
- Undercuts: The design should avoid undercuts or areas where the part has a shape that prevents it from being ejected from the mold. Undercuts require additional molding steps, such as slides or lifters, which can increase the cost and complexity of the mold.
- Material selection: The design should consider the type of plastic material that will be used for injection molding. Different materials have different properties, such as stiffness, strength, and temperature resistance, which can affect the design.
Materials
It involves the use of various types of plastic materials that are melted and injected into a mold to form a specific shape. The choice of material depends on the intended use of the final product, as well as its physical and chemical properties. Some of the materials commonly used include:
- Acrylonitrile Butadiene Styrene (ABS): ABS is a thermoplastic polymer that is known for its toughness, rigidity, and resistance to impact. It is commonly used in the production of automotive parts, toys, and electronic housings.
- Polycarbonate (PC): PC is a transparent thermoplastic polymer that is known for its high impact resistance and optical clarity. It is commonly used in the production of lenses, safety glasses, and electronic components.
- Polyethylene (PE): PE is a thermoplastic polymer that is known for its flexibility, toughness, and chemical resistance. It is commonly used in the production of packaging materials, pipes, and wire insulation.
- Polypropylene (PP): PP is a thermoplastic polymer that is known for its strength, flexibility, and resistance to heat. It is commonly used in the production of automotive parts, medical devices, and food packaging.
- Polystyrene (PS): PS is a thermoplastic polymer that is known for its clarity, stiffness, and low cost. It is commonly used in the production of packaging materials, disposable cups, and cutlery.
- Polyurethane (PU): PU is a thermoset polymer that is known for its flexibility, durability, and resistance to abrasion. It is commonly used in the production of automotive parts, footwear, and furniture.
Equipment
It requires specialized equipment to ensure that the final product meets the required specifications. Some of the key equipment used in precision plastic injection molding include:
- Injection molding machine: This is the main piece of equipment used in precision plastic injection molding. It consists of a hopper that holds the plastic material, a screw that melts and injects the plastic material into the mold, and a clamping unit that holds the mold in place.
- Mold: A mold is a precision tool that is used to shape the plastic material into the desired form. The mold consists of two halves, a core and a cavity, which are held together by the clamping unit of the injection molding machine.
- Heating and cooling systems: The heating system is used to melt the plastic material, while the cooling system is used to solidify the material in the mold. The cooling system typically consists of water channels that run through the mold to remove heat from the plastic material.
- Robots and automation systems: Robots and automation systems are used to handle the parts during the injection molding process. They can be programmed to remove the parts from the mold, trim excess material, and perform quality checks.
- Quality control equipment: Quality control equipment, such as cameras and sensors, is used to ensure that the final product meets the required specifications. They can be used to detect defects such as warping, sink marks, and voids.
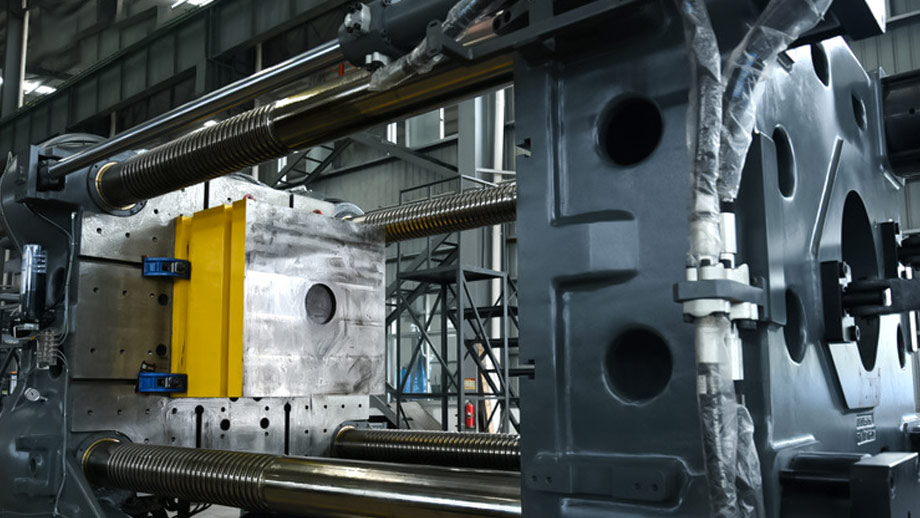
Quality Control in Precision Plastic Injection Molding
The following are some of the quality control measures used in precision plastic injection molding:
- Inspection of raw materials: Before any plastic material is used in the injection molding process, it is inspected to ensure that it meets the required specifications. This includes checking the color, shape, and physical properties of the material.
- Mold design and maintenance: The mold used in injection molding must be designed and maintained to meet the required specifications. This includes ensuring that the mold is properly cooled and that the mold cavity is free from any defects.
- Process control: The injection molding process must be carefully controlled to ensure that the plastic material is melted and injected into the mold at the correct temperature and pressure. This includes monitoring the injection speed, holding pressure, and cooling time.
- Inspection of finished products: Once the injection molding process is complete, the finished products are inspected to ensure that they meet the required specifications. This includes checking the dimensions, surface finish, and physical properties of the product.
- Documentation and traceability: All quality control measures must be documented to ensure that the final product can be traced back to its raw materials and manufacturing process. This includes recording the inspection results, process parameters, and any corrective actions taken.
Conclusion
Precision plastic injection molding is a highly specialized form of injection molding that offers several benefits over other manufacturing processes. The process involves several steps, including mold design, material preparation, injection molding, cooling and solidification, and ejection. Precision plastic injection molding is used in a variety of industries, including automotive, medical, consumer goods, and electronics. Designing for precision plastic injection molding requires careful consideration of several factors, including part geometry, wall thickness, draft angles, and undercuts. The selection of plastic material depends on several factors, including the intended use of the part, the required properties of the material, and the cost of the material. Quality control is critical in precision plastic injection molding to ensure that the parts produced meet the required specifications and standards.
Precision plastic injection molding has made outstanding contributions to high-precision products. Our experienced team utilizes state-of-the-art equipment to provide you with high-quality services. If you have any questions, welcome to contact us.