Liquid Silicone Rubber Injection Molding is a high-precision molding process that can produce silicone rubber products with complex shapes, high precision, and smooth surfaces. Its molding principle is to inject liquid silicone rubber into the mold and obtain the desired product after curing.
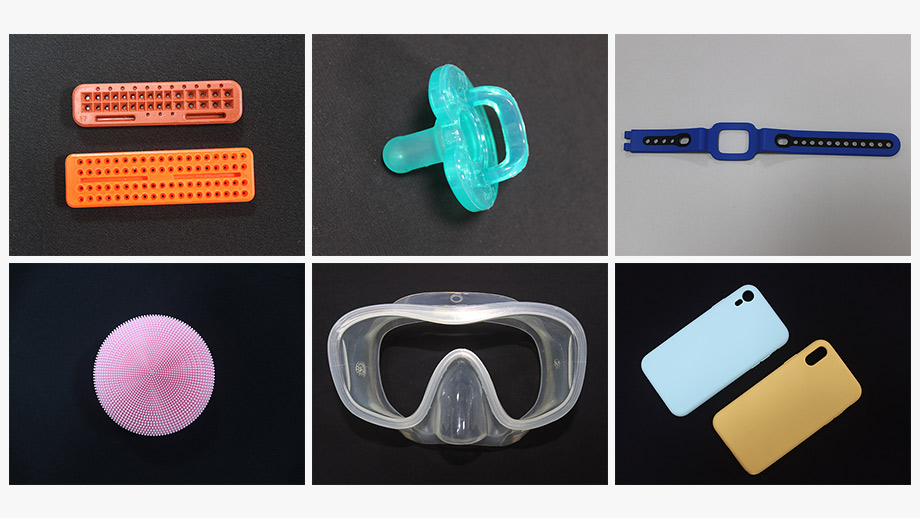
Our liquid silicone rubber (LSR) molding process can produce prototypes or end-use production parts in as little as 5 days. Our experienced team is always at your disposal to provide you with high-quality customized services.
Liquid silicone rubber is a high-performance material with excellent high-temperature resistance, low-temperature resistance, chemical corrosion resistance, wear resistance, aging resistance, and electrical insulation properties. It is widely used in electronics, electrical appliances, automobiles, medical treatment, molds, toys, handicrafts, and other fields.
The process of Liquid Silicone Rubber Injection Molding has the following characteristics:
- High precision: Liquid Silicone Rubber Injection Molding technology can produce high-precision silicone rubber products, and its precision can reach 0.01 mm, which can meet high-precision manufacturing requirements.
- Good reproducibility: It can reproduce the shape and surface details of the mold, ensuring the consistency and stability of the product.
- Good fluidity: It has good fluidity, which can fill every corner of the mold and make complex shapes.
- Good high-temperature resistance: Liquid silicone rubber has good high-temperature resistance and can be used for a long time in a high-temperature environment.
- Environmental protection and health: Liquid Silicone Rubber Injection Molding technology does not need to add any harmful substances, which meets the requirements of environmental protection and health.
Liquid Silicone Rubber Injection Molding technology is widely used, mainly in the following fields:
- Electronic and electrical field: Liquid silicone rubber can be used to manufacture seals, separators, conductive parts, insulating parts, etc. for electronic and electrical appliances. It has good high-temperature resistance, chemical corrosion resistance, aging resistance, and electrical insulation properties.
- Automotive field: Liquid silicone rubber can be used to manufacture automotive seals, sound-absorbing parts, shock-absorbing parts, heat-conducting parts, etc., and has good high-temperature resistance, low-temperature resistance, wear resistance, and aging resistance.
- Medical field: Liquid silicone rubber can be used to manufacture medical artificial organs, medical equipment, medical supplies, etc., and has good biocompatibility, high-temperature resistance, and chemical corrosion resistance.
- Handicraft field: liquid silicone rubber can be used to produce various handicrafts, such as figures, models, toys, etc., with good modeling performance and surface smoothness.
Liquid silicone rubber has the following types:
- Methyl liquid silicone rubber
Methyl liquid silicone rubber is a silicone rubber with a high crosslink density, which has excellent wear resistance, high-temperature resistance, chemical resistance, and electrical insulation properties. The material is often used to make high-quality seals, electronic components, automotive parts, and more.
- Polyester-based liquid silicone rubber
Polyester-based liquid silicone rubber is a silicone rubber with high transparency, high elasticity, and high wear resistance, which has excellent chemical resistance and high-temperature resistance. This material is usually used to manufacture high-precision molds, electronic components, medical devices, etc.
- Alkyl-based liquid silicone rubber
Alkyl-based liquid silicone rubber is a silicone rubber with excellent high-temperature resistance, chemical resistance, and abrasion resistance, which is highly flexible and elastic. The material is commonly used in the manufacture of high-temperature seals, electronic components, automotive components, and more.
It can be done by the following steps.
First, the manufacturer needs to prepare the liquid silicone rubber. This type of silicone rubber is usually composed of silane monomers and crosslinking agents, which cure quickly at room temperature to hard rubber. The quality and performance of silicone rubber depend on the type and ratio of silane monomer and crosslinking agent.
Next, the manufacturer needs to pour the liquid silicone rubber into the mold. A mold is a special tool that helps the manufacturer mold the liquid silicone rubber into the desired shape and size. Molds are usually made of metal, plastic, or rubber, and have the characteristics of high strength, high wear resistance, and high corrosion resistance.
Before pouring liquid silicone rubber into the mold, the manufacturer needs to treat the mold. This usually involves applying a release agent to the surface of the mold so that the molded silicone rubber can be easily removed from the mold. In addition, manufacturers also need to heat the mold to a certain temperature to promote the curing and crosslinking of silicone rubber.
Once the liquid silicone rubber is poured into the mold, it begins to cure and crosslink. During this process, the silane monomer and the crosslinking agent react chemically to form a crosslinked network structure. This network structure can make silicone rubber have the characteristics of high elasticity, high heat resistance, and high corrosion resistance.
Finally, the manufacturer needs to remove the silicone rubber from the mold for subsequent handling and processing. This usually involves steps such as trimming, sanding, and painting to get the silicone rubber into the desired shape and size. Once silicone rubber is fully processed and treated, it can be used in a variety of different applications.
In short, Liquid Silicone Rubber Injection Molding technology is a high-precision, high-efficiency, environmentally friendly, and healthy manufacturing process, which has broad application prospects. If you have custom needs, please contact us.