Computer numerical control (CNC) processing has revolutionized the manufacturing industry. It makes it easier to produce complex shapes and reduces the need for manual labor. However, the efficiency of CNC processing depends on the workflow. In this blog post, we will discuss how to optimize your CNC processing workflow for maximum efficiency.
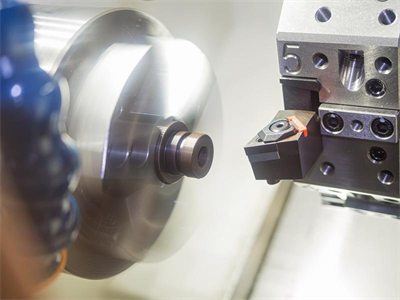
Minimize Material Waste
Material waste is a common problem in the manufacturing industry. It not only increases production costs but also affects the environment. To optimize your CNC processing workflow, you need to minimize material waste.
One way to minimize material waste is by using nesting software. Nesting software arranges parts on a sheet to minimize material waste. It also helps to reduce the number of cuts required for each part, which saves time. By using nesting software, you can optimize material usage and reduce the amount of scrap generated during the production process.
Another way to minimize material waste is by using the correct cutting tools. By using the right tools, you can increase the precision of your cuts and reduce the amount of material wasted. You should also consider the thickness of the material you are cutting and choose the appropriate cutting tool to minimize waste.
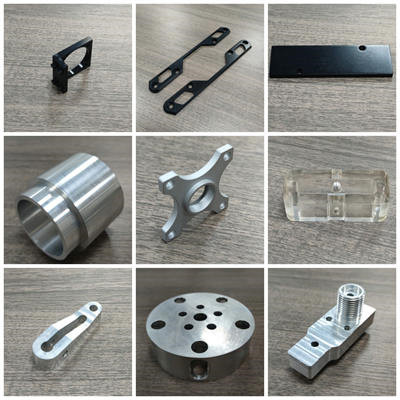
Use the Right Tools and Machines
Using the right tools and machines is essential for optimizing your CNC processing workflow. Outdated or inefficient machines can slow down the production process and affect product quality. Investing in high-quality machines not only increases efficiency but also reduces maintenance costs.
You should also ensure that you have the right tools for the job. Using the wrong tools can damage the material and affect product quality. By choosing the right tools and machines, you can optimize your workflow and reduce the risk of errors.
Streamline Your Workflow
Streamlining your workflow is another way to optimize your CNC processing workflow. You should analyze your current workflow and identify areas that can be improved.
For example, you can automate repetitive tasks such as tool changes and part loading. This reduces the need for manual labor and increases efficiency. You can also use software to track production progress and identify bottlenecks in the workflow. By streamlining your workflow, you can optimize your production process and reduce the risk of errors.
Conclusion
Optimizing your CNC processing workflow is essential for maximum efficiency. You can minimize material waste by using nesting software and the right cutting tools, use the right tools and machines, and streamline your workflow. By implementing these strategies, you can reduce production costs, increase efficiency, and improve product quality.
With the right approach to optimizing your CNC processing workflow, you can achieve maximum efficiency and productivity. By minimizing material waste, using the right tools and machines, and streamlining your workflow, you can enhance the quality of your products and reduce production costs. By implementing these strategies in your manufacturing process, you will be able to stay competitive in today’s fast-paced market.