Injection molding is a widely used manufacturing process for producing high-quality plastic parts. It involves injecting molten plastic into a mold cavity, where it cools and solidifies to form the final product. One of the most common defects that can occur during the injection molding process is the formation of bubbles in the molded parts. These bubbles can compromise the strength and integrity of the part, making it unsuitable for use in certain applications. This article will explore the causes of bubbles in injection molded parts and provide tips for eliminating them.

What Causes Bubbles in Injection Molded Parts?
There are several factors that can contribute to the formation of bubbles in injection molded parts. These include:
Inadequate Venting
Venting is a crucial part of the injection molding process, as it allows air and other gases to escape from the mold cavity as the molten plastic is injected. If the mold is not properly vented, air bubbles can become trapped within the plastic, leading to defects in the final part.
Inconsistent Melt Temperature
The temperature of the molten plastic is another important factor that can affect the formation of bubbles in injection molded parts. If the melt temperature is too high or too low, it can cause uneven flow of the plastic, leading to the formation of air pockets and other defects.
Poor Material Quality
The quality of the plastic material used in the injection molding process can also play a role in the formation of bubbles. If the material contains impurities or other contaminants, it can cause defects in the final part, including the formation of bubbles.
How to Eliminate Bubbles in Injection Molded Parts
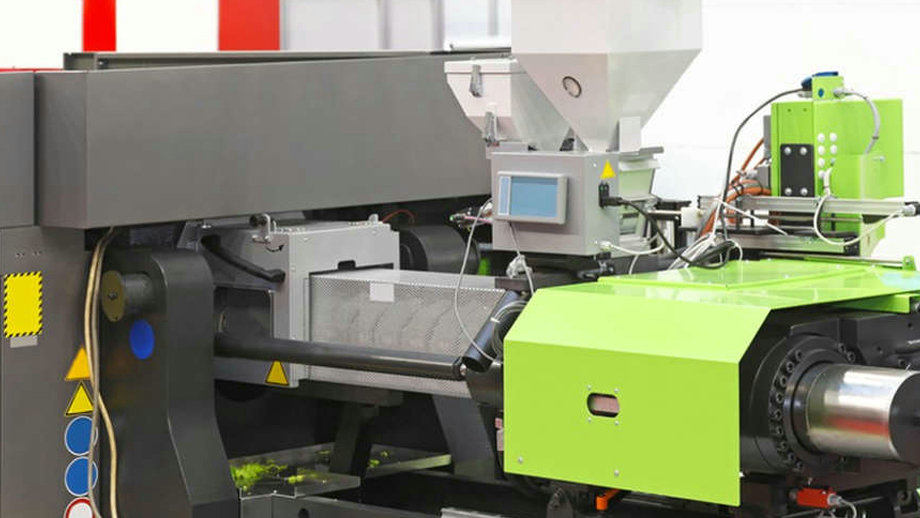
Fortunately, there are several steps that can be taken to eliminate bubbles in injection molded parts. These include:
Improve Venting
One of the most effective ways to eliminate bubbles in injection molded parts is to improve the venting of the mold. This can be achieved by adding additional vents or improving the existing ones to ensure that air and other gases can escape the mold cavity easily.
Optimize Melt Temperature
Optimizing the melt temperature of the plastic material can also help to eliminate bubbles in the final part. This can be achieved by adjusting the temperature of the barrel and nozzle of the injection molding machine to ensure that the plastic flows smoothly and evenly into the mold cavity.
Use High-Quality Materials
Using high-quality plastic material is another important step in eliminating bubbles in injection molded parts. Make sure that the material you are using is free from impurities and contaminants that can cause defects in the final part.
Reduce Injection Speed
Reducing the injection speed of the plastic material can also help to eliminate bubbles in the molded part. This can be achieved by adjusting the injection speed settings on the injection molding machine to ensure that the plastic flows smoothly and evenly into the mold cavity.
Conclusion
Bubbles in injection molded parts can be a frustrating and costly problem for manufacturers. However, by understanding the factors that contribute to their formation and taking steps to eliminate them, it is possible to produce high-quality parts that meet the needs of your customers. By improving venting, optimizing melt temperature, using high-quality materials, and reducing injection speed, you can eliminate bubbles in injection molded parts and produce parts that meet the highest standards of quality and performance. If you are experiencing problems with bubbles in your injection molded parts, contact JS Precision today to learn more about our injection molding services and how we can help you eliminate this common defect.