Extrusion Services
we offer custom–made extrusion solutions to meet your unique needs, ensuring the highest quality products and fast turnaround times.
- No MOQ
- We can customize parts according to your needs.
- Provide full-size quality inspection report
- Delivery on time, as fast as 3 days
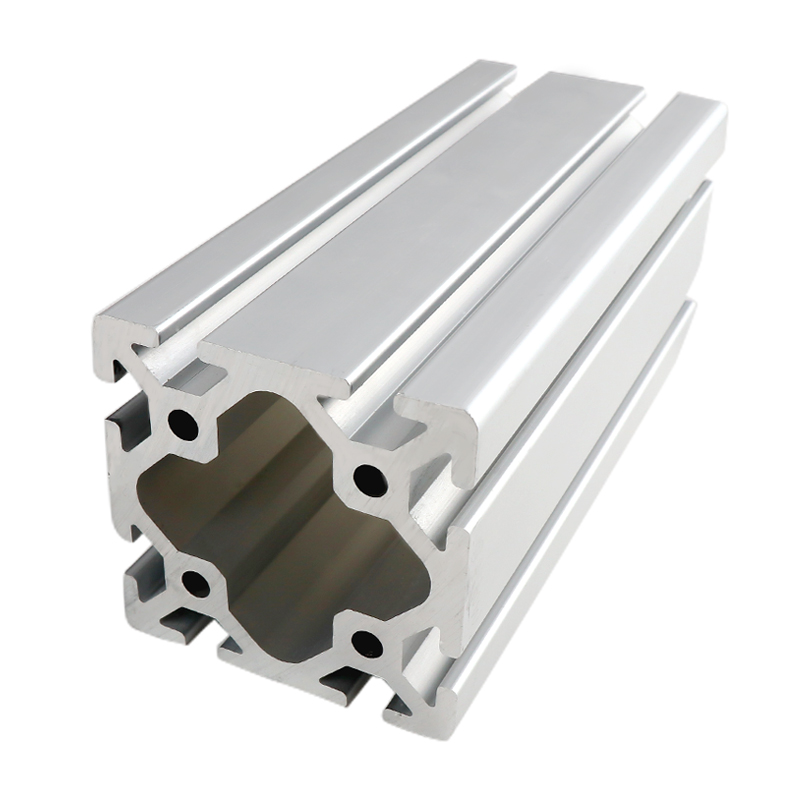
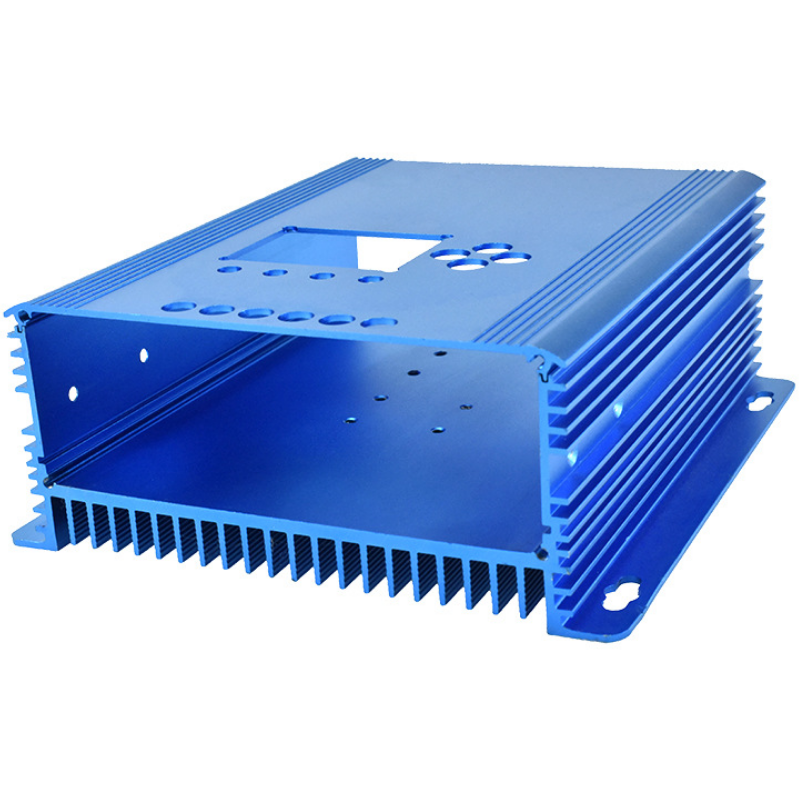
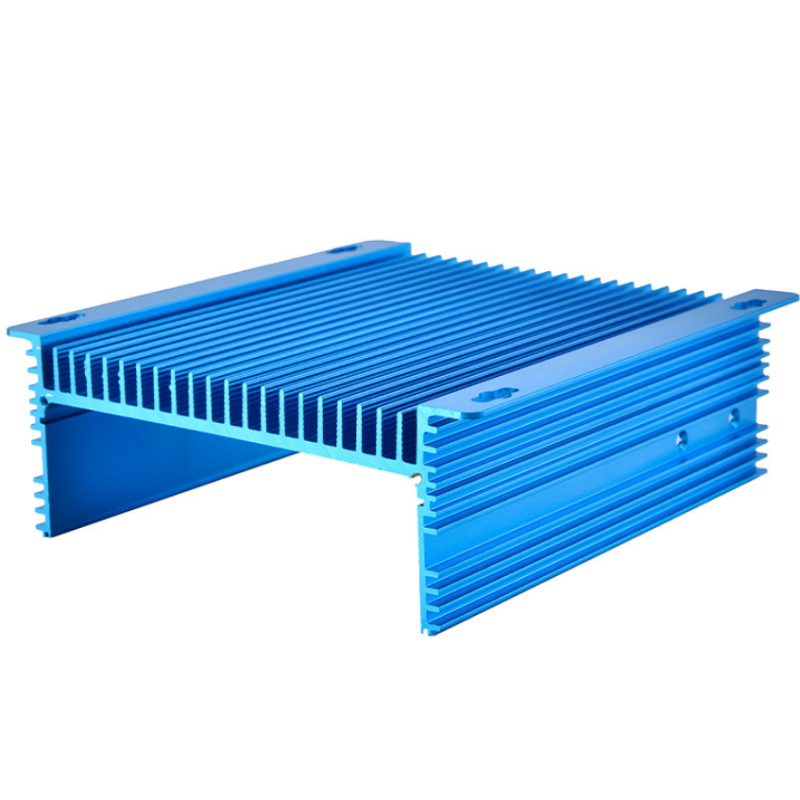
Our Extrusion Services
At JS Precision Technology, we provide a wide range of extrusion services to meet all of your needs. Our services include designing and manufacturing custom extrusions to meet exact specifications, as well as creating standard extrusions for many different applications. We specialize in producing high-quality plastic and metal extrusions, including aluminum, steel, and copper. We also have the capability to supply extrusions with a variety of coatings and finishes for superior performance.
Our experienced team of engineers and technicians provides top-notch service and support. We use state-of-the-art technology to ensure that our extrusions are accurate, durable, and efficient. We also provide complete design services to help you create the perfect extrusion for your application.
Whether you need a one-off custom extrusion or a large-scale production run, we have the resources to meet your needs. We provide quick turnaround times and competitive prices. Contact us today to learn more about how we can help you get the perfect extrusion for your project.
Extrusion Process:
Working Principle:
Extrusion is a simple compressive metal forming process. In this process, piston or plunger is used to apply compressive force at work piece. These process can be summarized as follow.
- First billet or ingot (metal work piece of standard size) is produced.
- This billet is heated in hot extrusion or remains at room temperature and placed into an extrusion press (An extrusion press is like a piston-cylinder device in which metal is placed in a cylinder and pushed by a piston. The upper portion of the cylinder is fitted with die).
- Now a compressive force is applied to this part by a plunger fitted into the press which pushes the billet towards the die.
- The die is a small opening of the required cross-section. This high compressive force allows the work metal to flow through a die and convert into desired shape.
- Now the extruded part remove from the press and is heat treated for better mechanical properties.
This is basically the working of the extrusion process.
Types of Extrusion:
Extrusion process can be classified into the following types.
According to the direction of flow of metal
Direct Extrusion:
In this type of extrusion process, metal is forced to flow in the direction of the feed or the punch. The punch moves toward the die during extrusion. This process required higher force due to higher friction between the billet and the container.
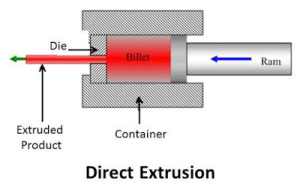
Indirect Extrusion:
In this process, metal is flow in the opposite direction of the plunger movement. The die is fitted at the opposite side of the punch movement. In this process, the metal is allowed to flow through the annular space between the punch and the container.
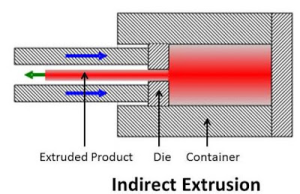
Hydrostatic Extrusion:
This process uses fluid to apply pressure on the billet. In this process, friction is eliminated because the billet is neither in contact with the cylinder wall nor the plunger. There is fluid between the billet and the plunger. The plunger applies force on fluid which is further applied to the billet. Normally vegetable oils are used as the fluid. This process is accomplished by leakage problems and uncontrolled speed of extrusion.
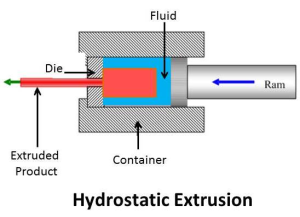
According to the working temperature
Hot Extrusion:
If the extrusion process takes place above recrystallization temperature which is about 50-60% of its melting temperature, the process is known as hot extrusion.
Advantages:
- Low force required compare to cold working.
- Easy to work in hot form.
- The product is free from stain hardening.
Disadvantages:
- Low surface finish due to scale formation on extruded part.
- Increase die wear.
- High maintenance required.
Cold Extrusion:
If the extrusion process takes place below crystallization temperature or room temperature, the process is known as cold extrusion. Aluminum cans, cylinder, collapsible tubes etc. are example of this process.
Advantages:
- High mechanical properties.
- High surface finish
- No oxidation at metal surface.
Disadvantages:
- High force required.
- Product is accomplished with strain hardening.
Application:
- Extrusion is widely used in production of tubes and hollow pipes.
- Aluminum extrusion is used in structure work in many industries.
- This process is used to produce frames, doors, window etc. in automotive industries.
- Extrusion is widely used to produce plastic objects.
Advantages and Disadvantages:
Advantages:
- High extrusion ratio (It is the ratio of billet cross section area to extruded part cross section area).
- It can easily create complex cross section.
- This working can be done with both brittle and ductile materials.
- High mechanical properties can achieved by cold extrusion.
Disadvantages:
- High initial or setup cost.
- The high compressive force required.
Frequently Asked Questions about Extrusion
We provide new product developers with engine processing parts suitable for functional testing or final use of engineering -level materials. Get your required Extrusion support by reading FAQ.
We do not have a minimum order quantity. Whether you need a single part or thousands of parts, we are happy to work with you.
We use a variety of processes, including CNC milling, turning, sheet metal fabrication, metal extrusion, die casting, metal stamping, and spring machining. Each process is chosen based on the specific requirements of the part in question.
We offer a variety of finishes, including anodizing, plating, powder coating, and painting. If you have a specific finish requirement, please let us know and we will do our best to accommodate your needs.
Our lead time varies depending on the complexity and quantity of the parts being manufactured. We will provide you with an estimated lead time when you submit your order, and we will keep you informed throughout the manufacturing process.
We have a rigorous quality control process that involves multiple inspections and tests throughout the manufacturing process. We use advanced inspection and testing equipment to ensure that all parts meet or exceed industry standards.
We work with a variety of materials, including aluminum, brass, copper, stainless steel, and titanium. If you have a specific material requirement, please let us know and we will do our best to accommodate your needs.
Our pricing is based on the complexity and quantity of the parts being manufactured. We will provide you with a detailed quote when you submit your order.
Yes, we have a team of experienced engineers who can assist you with design and prototyping. We can work with you to optimize your designs for manufacturability and efficiency.
We offer a warranty on all of our products. If you experience any issues with our products, please contact us and we will work with you to resolve the issue.
You can submit an order by contacting us directly or through our website. We will work with you to ensure that your order is submitted correctly and that you receive the parts you need on time and within budget.