As a professional injection molding manufacturer, JS Precision knows that even the most well-crafted parts can sometimes have defects. These manufacturing defects can have a significant impact on the functionality and quality of the product, leading to costly rework or even product recalls. In this article, we’ll explore 10 common injection molding defects and their solutions, so you can prevent them from occurring in your products.
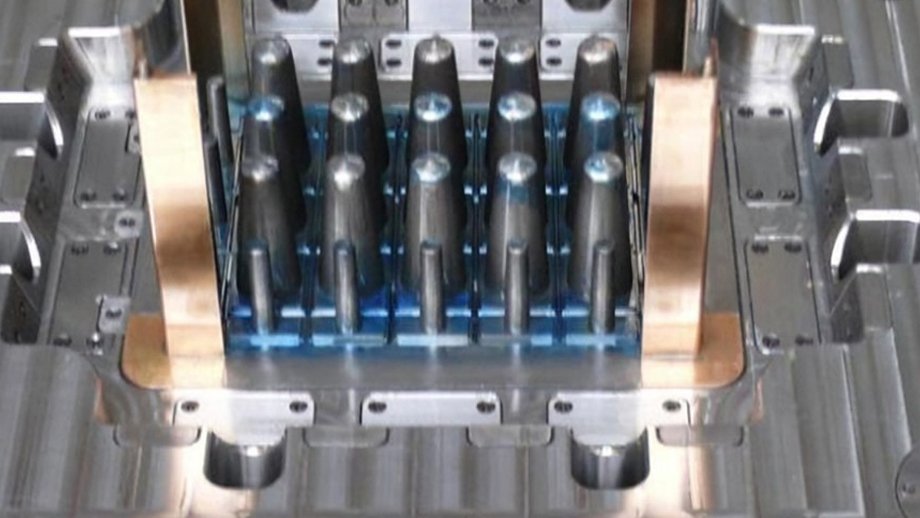
- Flash – This defect occurs when excess material leaks from the mold and creates a thin, unwanted layer. The solution is to adjust the clamping force, reduce injection speed, or increase cooling time.
- Short Shots – This defect happens when the mold doesn’t fill completely, leaving a void or incomplete part. The solution is to adjust the injection pressure, increase the injection time, or check for blocked cavities.
- Sink Marks – These are depressions or dents on the surface of the part caused by uneven cooling or insufficient packing pressure. The solution is to adjust the packing pressure, increase cooling time, or modify the design to redistribute the material.
- Warping – This defect is characterized by a bent or twisted part caused by uneven cooling or improper mold temperature. The solution is to adjust the mold temperature, increase cooling time, or modify the design to reduce stress concentration.
- Burn Marks – These are dark spots or streaks caused by excessive heat or overheating the material. The solution is to reduce the injection speed, adjust the temperature, or increase ventilation.
- Jetting – This defect is caused by material flowing too quickly through the mold, resulting in a visible seam or mark. The solution is to adjust the gate size, reduce injection speed, or increase mold temperature.
- Weld Lines – These are visible lines or marks caused by the merging of two or more flow fronts. The solution is to modify the gate location, reduce injection speed, or increase material temperature.
- Bubbles – These are air pockets or voids within the material caused by trapped air or excessive moisture. The solution is to increase drying time, adjust the material temperature, or change the material grade.
- Flow Lines – These are visible lines or streaks on the surface of the part caused by the flow of material through the mold. The solution is to adjust the mold temperature, reduce injection speed, or increase pressure.
- Voids – These are empty spaces or gaps within the material caused by trapped air or improper packing pressure. The solution is to increase packing pressure, adjust the cooling time, or modify the design to eliminate thick sections.
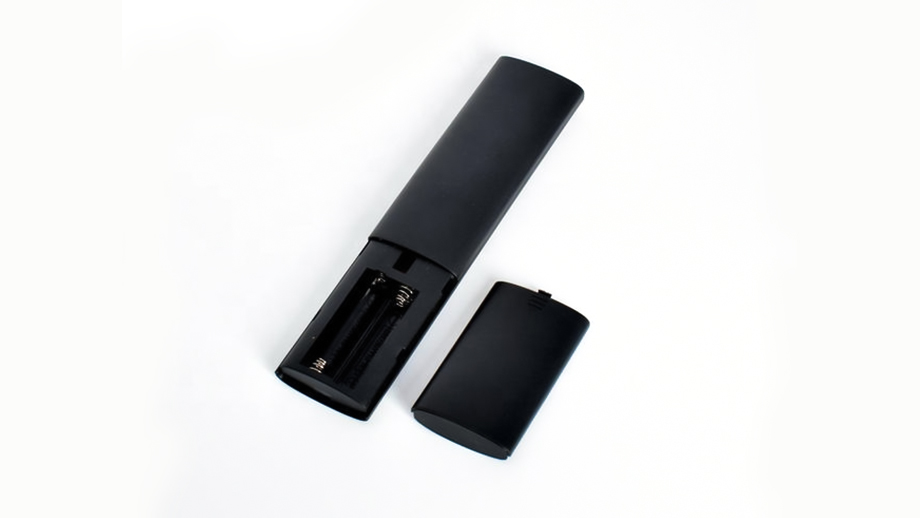
At JS Precision, we understand that preventing injection molding defects requires a combination of experience, expertise, and attention to detail. Our team of skilled engineers and technicians is committed to delivering high-quality, defect-free parts that meet your exact specifications. Contact us today to learn more about our injection molding services and how we can help you achieve your manufacturing goals.