Sheet metal processing is an important aspect of modern manufacturing, and it involves the manipulation of thin sheets of metal to create a range of products and components. This article will explore the common processing methods and tools used in sheet metal processing, providing insight into the techniques that enable manufacturers to create high-quality products efficiently and effectively.
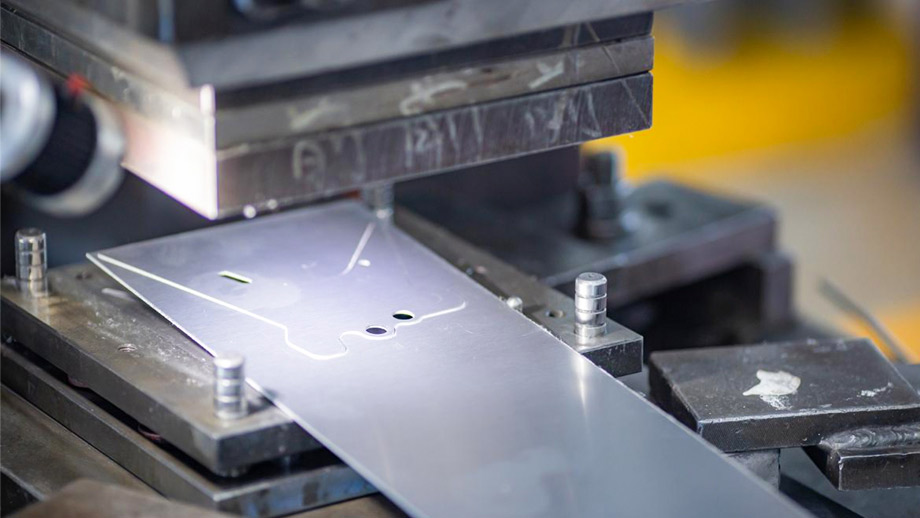
Overview of Sheet Metal Processing
Sheet metal is a highly versatile material that can be used to create a wide range of products, including automotive components, electrical enclosures, and household appliances. Sheet metal processing involves several key steps, including cutting, bending, forming, and finishing.
The first step in sheet metal processing is cutting, which involves the use of cutting tools to remove excess material from the sheet. This can be done using a range of tools, including laser cutters, plasma cutters, and waterjet cutters. Laser cutters are particularly popular due to their high precision and speed, while waterjet cutters are ideal for cutting thicker materials.
Once the sheet metal has been cut to size, it can be bent and formed into the desired shape. This is typically done using press brakes or roll forming machines, which apply pressure to the metal to achieve the desired shape. Sheet metal can also be formed using dies and punches, which are used to cut and shape the metal into specific shapes and sizes.
Finally, sheet metal products are finished using a range of techniques, including painting, powder coating, and anodizing. These techniques help to protect the metal from corrosion and improve its appearance, making it more attractive to consumers.
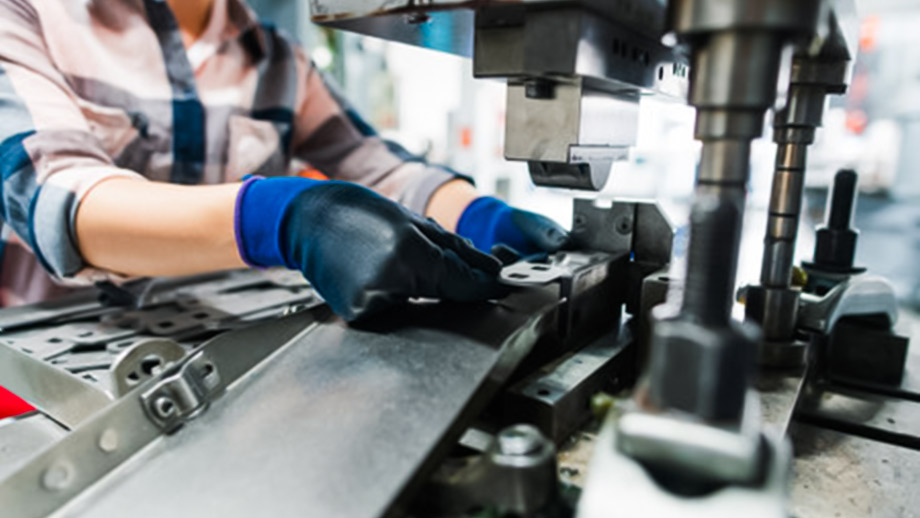
Common Sheet Metal Processing Tools
There are a wide range of tools and equipment used in sheet metal processing, each with its own unique benefits and limitations. Some of the most common tools used in sheet metal processing include:
- Press Brakes: Press brakes are machines that use a hydraulic ram to apply pressure to sheet metal, bending it into the desired shape. They are ideal for creating precise bends and angles in sheet metal.
- Roll Forming Machines: Roll forming machines are used to shape sheet metal into cylindrical or curved shapes. They work by passing the metal through a series of rollers, gradually bending it into the desired shape.
- Laser Cutters: Laser cutters use a high-powered laser to cut through sheet metal with a high degree of precision. They are ideal for cutting intricate shapes and patterns.
- Plasma Cutters: Plasma cutters use a high-temperature plasma arc to cut through sheet metal. They are particularly effective at cutting thicker materials.
- Waterjet Cutters: Waterjet cutters use a high-pressure stream of water to cut through sheet metal. They are ideal for cutting thicker materials and can be used to cut a wide range of materials, including metal, stone, and glass.
- Dies and Punches: Dies and punches are used to cut and shape sheet metal into specific shapes and sizes. They are particularly useful for creating complex shapes and patterns.
Conclusion
In conclusion, sheet metal processing is a complex and highly sophisticated industry that relies on a range of tools and techniques to create high-quality products. By understanding the common processing methods and tools used in sheet metal processing, manufacturers can ensure that they are using the most efficient and effective techniques to create the products their customer’s demand. At JS Precision, we specialize in sheet metal processing, and we have the expertise and experience to deliver high-quality products that meet the needs of our clients. Contact us today to learn more about our services and how we can help you achieve your goals.