Injection molding is a manufacturing process that involves injecting molten plastic material into a mold. The material then cools and hardens, resulting in a solid plastic part that can be used for a wide range of purposes. Injection molds play a crucial role in this process, as they determine the shape and size of the final product. In this article, we will discuss the different types of injection molds and their applications.
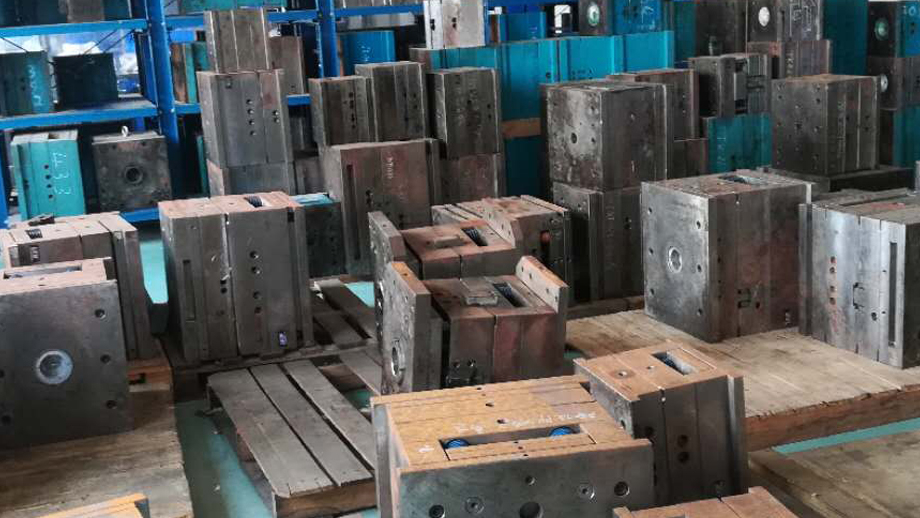
- Single-cavity molds
Single-cavity molds are the simplest type of injection molds. They consist of a single cavity that is used to produce a single part at a time. These molds are ideal for low-volume production runs and prototypes. They are also less expensive than other types of molds, making them a good choice for small businesses and startups.
- Multi-cavity molds
Multi-cavity molds have multiple cavities that can be used to produce multiple parts at the same time. These molds are ideal for high-volume production runs, as they can produce large quantities of parts quickly and efficiently. They are also more expensive than single-cavity molds, but the cost is offset by the increased production speed and volume.
- Family molds
Family molds are a type of multi-cavity mold that is used to produce multiple parts that are related to each other. For example, a family mold can be used to produce a set of parts that are used in the same product. Family molds are ideal for products that require multiple parts, as they can produce all of the parts at the same time, reducing production time and costs.
- Hot runner molds
Hot runner molds use a heating system to keep the plastic material in the mold at a consistent temperature. This eliminates the need for runners, which are used to channel the plastic material to the cavities in the mold. Hot runner molds are ideal for large and complex parts that require precise molding, as they can produce parts with minimal waste and reduced cycle times.
- Cold runner molds
Cold runner molds use runners to channel the plastic material to the cavities in the mold. The runners are then removed from the final product, resulting in waste material. Cold runner molds are ideal for low-volume production runs and prototypes, as they are less expensive than hot runner molds.
- Insert molds
Insert molds are used to insert preformed components, such as metal or plastic parts, into the plastic part during the molding process. This allows for the creation of complex parts that require multiple components. Insert molds are ideal for products that require high precision and accuracy, as they can produce parts with minimal waste.
- Overmolding molds
Overmolding molds are used to produce parts that have multiple layers of plastic material. This is achieved by injecting the first layer of plastic material into the mold, and then injecting a second layer over the first layer. Overmolding molds are ideal for products that require multiple materials, such as soft and hard plastics.
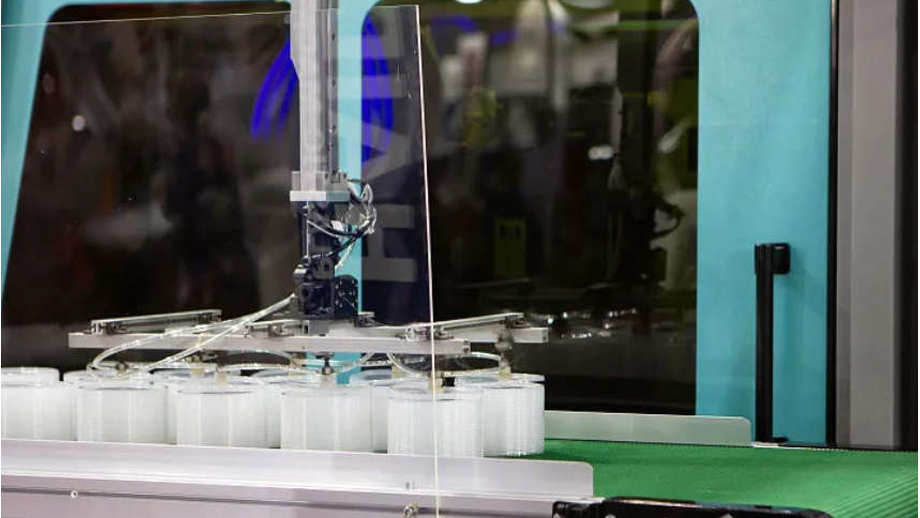
In conclusion, injection molds play a crucial role in the injection molding process. Understanding the different types of injection molds and their applications can help businesses choose the right mold for their production needs. At JS Precision, we specialize in high-quality injection molds that are designed to meet the unique needs of our customers. Contact us today to learn more about our injection molding services and how we can help you with your production needs.