Injection molding is a widely used manufacturing process used to produce plastic parts of different shapes and sizes. The process involves injecting molten plastic material into a mold cavity, allowing it to cool and solidify, and then ejecting the finished product. However, injection molded shell parts may sometimes exhibit unstable color, which can affect the quality of the final product.
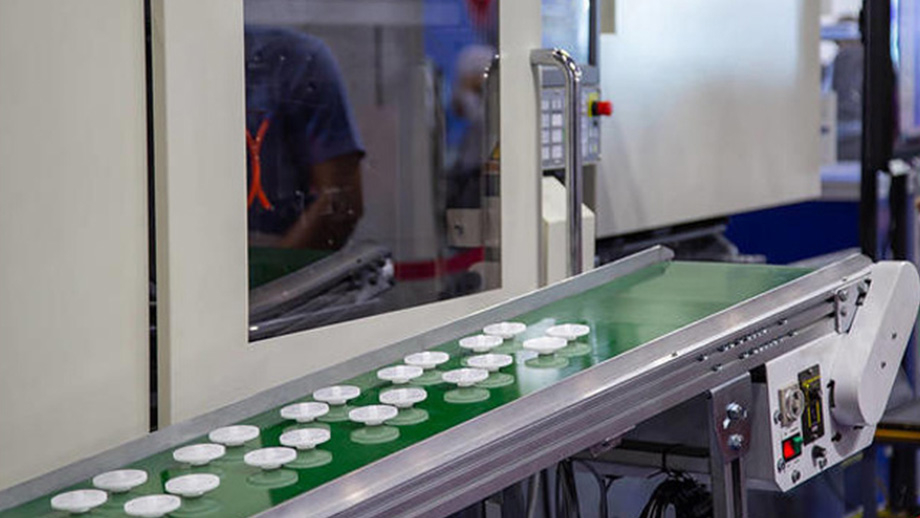
In this article, we will analyze the eight causes of the unstable color of injection-molded shell parts and discuss how to prevent and address these issues.
- Inconsistent Material Quality
One of the leading causes of unstable color in injection molded shell parts is inconsistent material quality. The color of the finished product may vary if the quality of the raw material used is not uniform. This can be due to variations in the raw material composition, impurities, or contamination. To prevent this issue, manufacturers should use high-quality raw materials from reliable suppliers and conduct quality control checks regularly.
- Inadequate Mixing of Colorants
Another cause of unstable color in injection molded shell parts is inadequate mixing of colorants. If the colorant is not mixed properly, it can lead to uneven distribution of color in the finished product. To address this issue, manufacturers should ensure that the colorant is thoroughly mixed with the raw material before the injection molding process.
- Inconsistent Melt Temperature
Inconsistent melt temperature is another common cause of unstable color in injection molded shell parts. If the melt temperature is not consistent, it can cause variations in the color of the finished product. To prevent this issue, manufacturers should maintain a consistent melt temperature throughout the injection molding process.
- Inadequate Cooling Time
Inadequate cooling time can also cause unstable color in injection molded shell parts. If the cooling time is too short, it can cause incomplete solidification of the material, which can result in uneven color distribution. To address this issue, manufacturers should ensure that the cooling time is sufficient for the specific material and part being produced.
- Inconsistent Injection Speed and Pressure
Inconsistent injection speed and pressure can also cause unstable color in injection molded shell parts. If the injection speed and pressure are not consistent, it can cause variations in the color of the finished product. To prevent this issue, manufacturers should maintain a consistent injection speed and pressure throughout the injection molding process.
- Poor Mold Design
Poor mold design can also contribute to unstable color in injection-molded shell parts. If the mold design is not optimized for the specific material and part being produced, it can cause variations in the color of the finished product. To address this issue, manufacturers should work with experienced mold designers to develop molds that are optimized for the specific material and part being produced.
- Inadequate Maintenance of Injection Molding Equipment
Inadequate maintenance of injection molding equipment can also cause unstable color in injection molded shell parts. If the equipment is not properly maintained, it can lead to variations in the color of the finished product. To prevent this issue, manufacturers should conduct regular maintenance checks and repairs on their injection molding equipment.
- Environmental Factors
Environmental factors, such as temperature and humidity, can also contribute to unstable color in injection molded shell parts. If the temperature and humidity are not controlled, it can cause variations in the color of the finished product. To prevent this issue, manufacturers should ensure that the injection molding process is conducted in a controlled environment with consistent temperature and humidity levels.
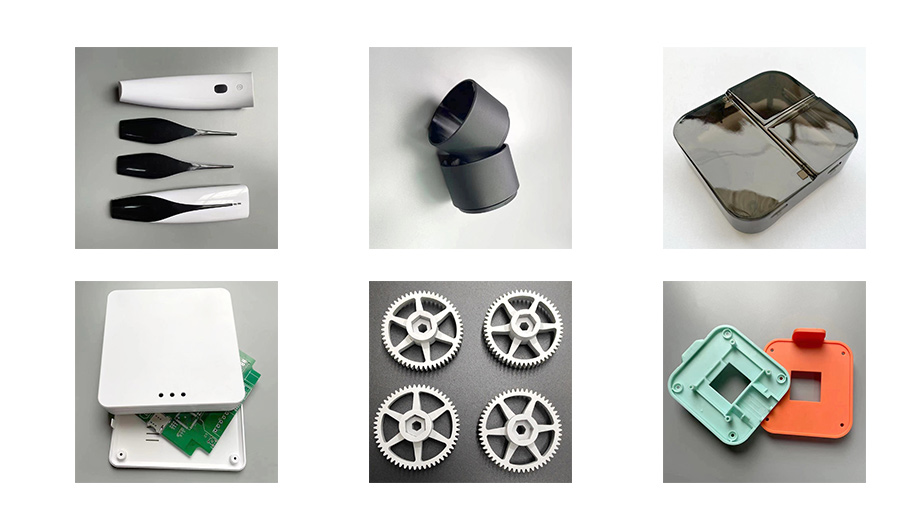
In conclusion, unstable color in injection molded shell parts can be caused by a variety of factors, including inconsistent material quality, inadequate mixing of colorants, inconsistent melt temperature, inadequate cooling time, inconsistent injection speed and pressure, poor mold design, inadequate maintenance of injection molding equipment, and environmental factors. By addressing these issues, manufacturers can produce high-quality injection molded shell parts with consistent color and improved overall quality.