Injection molding is a widely used manufacturing process that involves the production of plastic parts by injecting molten plastic into a mold. However, injection-molded products often suffer from cracking, which can significantly compromise their performance and structural integrity. In this article, we will explore the causes of cracking in injection-molded products and discuss some measures that can be taken to prevent it.
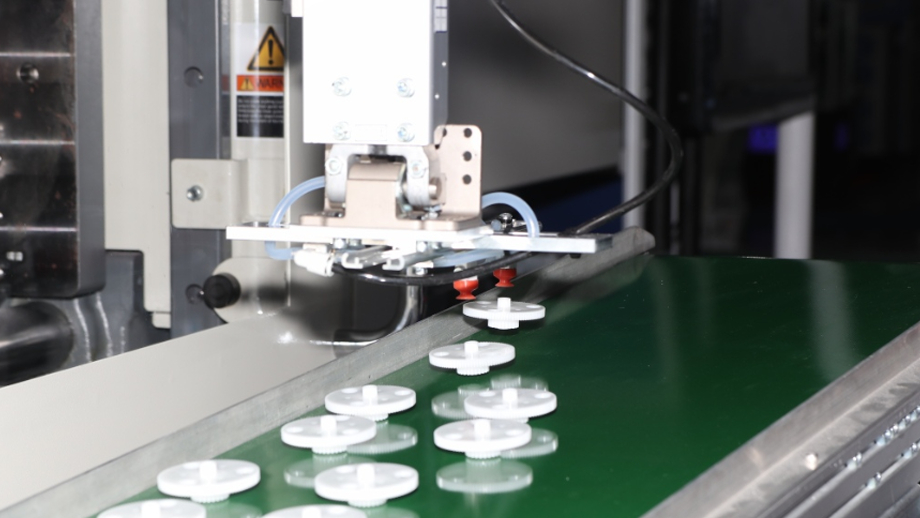
What is Cracking?
Cracking is a phenomenon in which an injection molded product develops one or more visible cracks on its surface or within its structure. Cracks can be caused by a range of factors, including the properties of the plastic material, the design of the mold, and the injection molding process itself. Cracks can be classified into two main types: surface cracks and internal cracks.
Surface cracks are visible cracks that occur on the surface of the product. They can be caused by stress concentration, material degradation, or poor mold design. Internal cracks, on the other hand, are cracks that occur within the structure of the product. They can be caused by improper cooling or packing, uneven polymer flow, or material degradation.
Causes of Cracking
There are several factors that can contribute to the development of cracks in injection-molded products. Some of the most common causes of cracking include:
- Material Properties
The properties of the plastic material used for injection molding can have a significant impact on the likelihood of cracking. Some materials are more prone to cracking than others, especially if they are subjected to high stress or temperature. In addition, the presence of impurities or contaminants in the material can also increase the risk of cracking.
- Mold Design
The design of the mold can also play a role in the development of cracks. Poor mold design can result in stress concentration, which can cause surface cracks to form. In addition, if the mold is not properly vented, it can trap gas or moisture inside the product, which can lead to internal cracks.
- Injection Molding Process
The injection molding process itself can also contribute to the development of cracks. If the cooling rate is too fast or too slow, it can cause internal stresses to build up, which can result in cracking. In addition, if the packing pressure is too high or too low, it can also cause cracking.
Prevention Measures
There are several measures that can be taken to prevent cracking in injection molded products. Some of the most effective measures include:
- Material Selection
Choosing the right plastic material for the application is crucial for preventing cracking. It is important to select a material that has the appropriate properties for the intended use and to avoid materials that are prone to cracking.
- Mold Design
Proper mold design is critical for preventing cracking. Mold designers should pay attention to the thickness and geometry of the product, as well as the placement of gates and vents. In addition, the mold should be properly vented to prevent the accumulation of gas or moisture.
- Injection Molding Process
The injection molding process should be carefully controlled to prevent cracking. Proper cooling and packing pressure are key factors in preventing internal stress buildup. In addition, the injection speed and temperature should be optimized for the specific material and product.
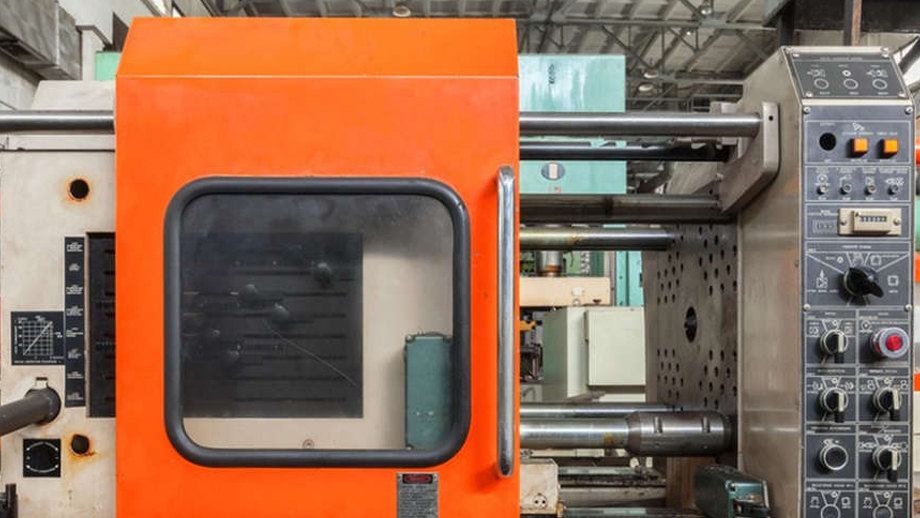
Conclusion
Cracking is a common problem in injection molding, but it can be prevented by taking the appropriate measures. By carefully selecting the plastic material, designing the mold properly, and controlling the injection molding process, it is possible to produce high-quality products that are free from cracks. As a leading injection molding manufacturer, JS Precision is committed to providing our customers with the highest quality products and services. If you have any questions or would like to learn more about our injection molding capabilities, please contact us today.