Injection molding is a popular manufacturing process used to create a range of plastic products. However, even the most well-designed and carefully produced parts can experience cracking. This can be caused by a range of factors, from material selection to design flaws. In this article, we will explore what you should do if your injection molded parts crack, and how you can prevent this issue from happening in the future.
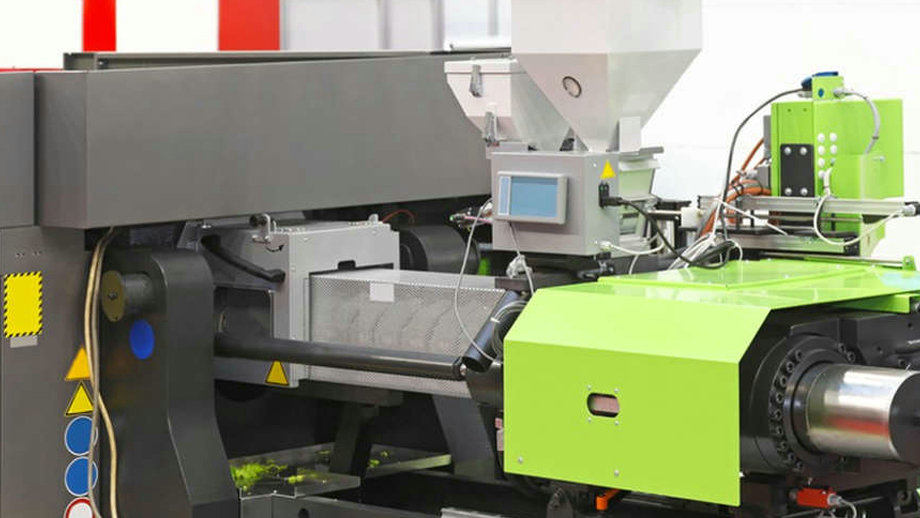
What Causes Injection Molded Parts to Crack?
Before we dive into what to do when your injection molded parts crack, it’s important to understand what causes this issue. There are several factors that can contribute to cracking, including:
- Material selection: Choosing the wrong material can result in parts that are too brittle or prone to cracking. It’s important to select a material that is appropriate for the intended use of the part.
- Design flaws: Poor design can result in parts that are too thin or have sharp corners, which can cause stress and lead to cracking.
- Processing issues: Improper processing techniques, such as incorrect temperature or pressure settings, can result in parts that are more prone to cracking.
What to Do When Your Injection Molded Parts Crack
If you discover that your injection molded parts have cracked, there are a few steps you can take to address the issue:
- Identify the cause: Before you can fix the problem, you need to understand what caused it. Take a close look at the cracked part to determine if the issue was caused by material selection, design flaws, or processing issues.
- Adjust the design: If the cracking was caused by design flaws, you may need to adjust the design of the part. This could involve making the part thicker or changing the shape to reduce stress points.
- Adjust processing settings: If the issue was caused by processing issues, you may need to adjust the temperature, pressure, or other settings to ensure that the parts are being produced properly.
- Consider a different material: If the issue was caused by material selection, you may need to consider using a different material that is better suited to the intended use of the part.
- Contact a professional: If you are unsure of how to address the issue, or if the cracking is severe, it may be best to contact a professional injection molding company for assistance.
Preventing Injection Molded Parts from Cracking
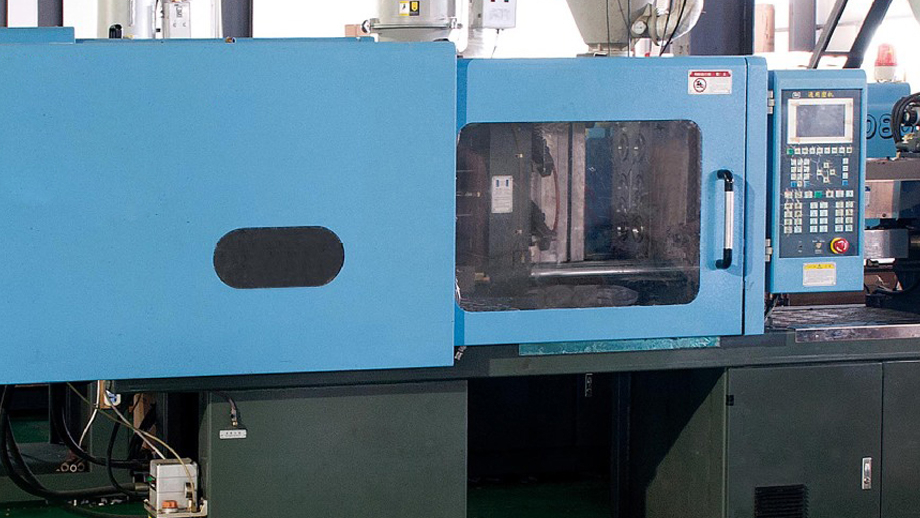
While it’s important to know what to do when your injection molded parts crack, it’s even better to prevent this issue from happening in the first place. Here are some steps you can take to prevent cracking:
- Use appropriate materials: Make sure you are using a material that is appropriate for the intended use of the part. This can help reduce the likelihood of cracking.
- Optimize design: Design your parts to minimize stress points and avoid sharp corners. This can help reduce stress and prevent cracking.
- Optimize processing settings: Ensure that your injection molding machine is properly calibrated and that you are using the correct temperature, pressure, and other settings.
- Work with a professional injection molding company: A professional injection molding company can help ensure that your parts are designed and produced properly, reducing the risk of cracking.
Conclusion
Injection molding is a popular manufacturing process, but even the best-designed parts can experience cracking. By understanding what causes cracking and taking steps to prevent it, you can ensure that your parts are produced to the highest standard. If you do experience cracking, take the time to identify the cause and take appropriate steps to address the issue. With the right approach, you can minimize the risk of cracking and ensure that your injection molded parts are of the highest quality.