Introduction
As a professional injection molding manufacturer, JS Precision is committed to providing high-quality products and services to its customers. One of the most common issues that injection molding manufacturers face is the insufficient filling of products. This issue can result in defective products and ultimately lead to customer dissatisfaction. In this blog post, we will analyze 15 reasons for insufficient filling of injection molding products and provide solutions to prevent this issue.
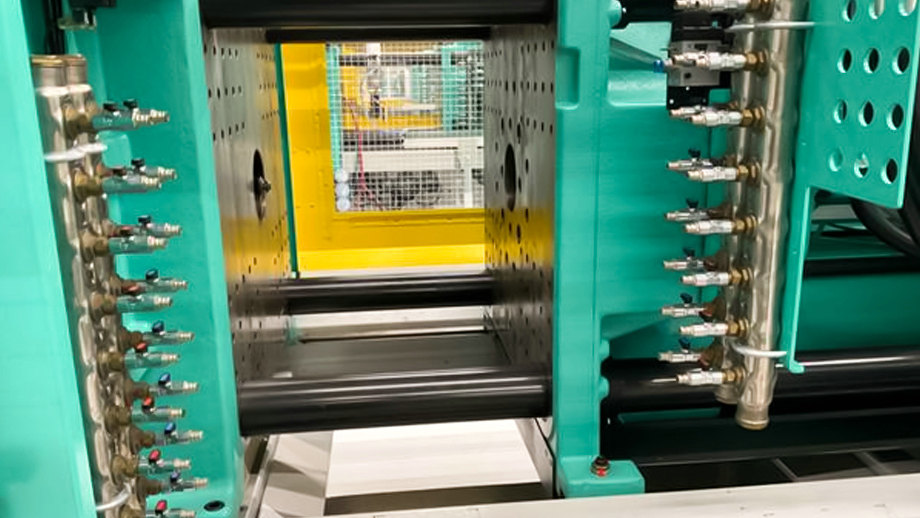
Reasons
- Improper Gate Location: The gate location plays a crucial role in the filling process. The gate should be placed in a location that allows the molten plastic to flow smoothly into the mold cavity. If the gate is placed in an improper location, it can lead to insufficient filling.
- Inadequate Injection Pressure: Injection pressure is the force that pushes the molten plastic into the mold cavity. If the injection pressure is inadequate, the molten plastic will not fill the mold cavity completely.
- Short Shot: A short shot occurs when the molten plastic does not fill the mold cavity completely. This can happen due to insufficient injection pressure, improper gate location, or a clogged sprue.
- Cold Runner: A cold runner is a channel that connects the nozzle of the injection molding machine to the mold cavity. If the cold runner is too cold, it can cause the molten plastic to solidify before it reaches the mold cavity, leading to insufficient filling.
- Improper Plastic Flow: The flow of the molten plastic should be smooth and even. If the plastic flow is uneven, it can lead to insufficient filling.
- Poor Venting: Proper venting is essential to allow air to escape from the mold cavity. If the mold is not vented properly, it can cause air traps, leading to insufficient filling.
- Insufficient Holding Pressure: Holding pressure is the pressure that keeps the molten plastic in the mold cavity until it solidifies. If the holding pressure is insufficient, the molten plastic can shrink before it solidifies, leading to insufficient filling.
- Improper Mold Temperature: The mold temperature should be maintained at a consistent level. If the mold temperature is too low, it can cause the molten plastic to solidify before it reaches the mold cavity, leading to insufficient filling.
- Improper Injection Speed: Injection speed is the speed at which the molten plastic is injected into the mold cavity. If the injection speed is too slow, it can lead to insufficient filling.
- Improper Barrel Temperature: The barrel temperature should be maintained at a consistent level. If the barrel temperature is too low, it can cause the molten plastic to solidify before it reaches the mold cavity, leading to insufficient filling.
- Improper Screw Speed: The screw speed should be adjusted according to the type of plastic being used. If the screw speed is too low, it can lead to insufficient filling.
- Inadequate Cooling Time: Cooling time is the time it takes for the molten plastic to solidify in the mold cavity. If the cooling time is inadequate, it can cause the molten plastic to shrink before it solidifies, leading to insufficient filling.
- Improper Wall Thickness: The wall thickness of the product should be uniform. If the wall thickness is uneven, it can lead to insufficient filling.
- Improper Design of the Mold: The mold design should be optimized for the type of plastic being used. If the mold design is improper, it can lead to insufficient filling.
- Poor Maintenance of the Injection Molding Machine: Regular maintenance of the injection molding machine is essential to prevent issues such as insufficient filling.
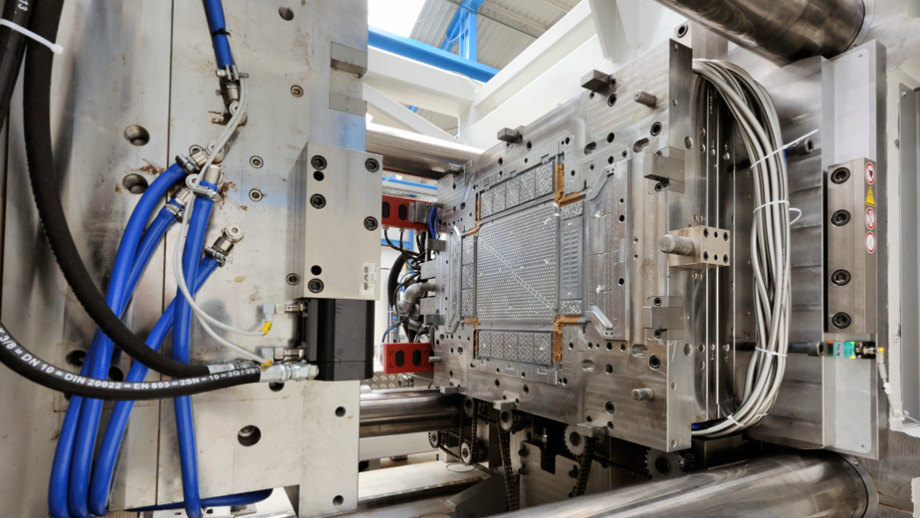
In conclusion
Insufficient filling of injection molding products can be caused by various factors. It is important to identify the root cause of the issue and take appropriate measures to prevent it. At JS Precision, we prioritize quality and customer satisfaction. Contact us to learn more about our injection molding services.