3D printing is revolutionizing the consumer goods sector by enabling the production of innovative and personalized products. This cutting-edge technology empowers companies to fabricate diverse items, including bespoke furniture, customized bicycles, distinctive wearables, and tailored eyewear, with unparalleled accuracy and customization. The advent of industrial 3D printers signifies a substantial progression in manufacturing, presenting economic efficiency, swift production, and the versatility to generate intricate designs that traditional methods cannot achieve.
In this discourse, we will delve into the transformative impact of 3D printing on consumer goods manufacturing, underscoring its potential for detailed designs and resilience. We will also discuss ideal materials and printers for this innovative manufacturing process. The spotlight is on the way 3D printing is reshaping the consumer products sector by facilitating the fabrication of tailor-made, superior-quality items that cater to the evolving needs of consumers.
Revolutionizing Manufacturing: The Dawn of 3D Printing in Consumer Goods
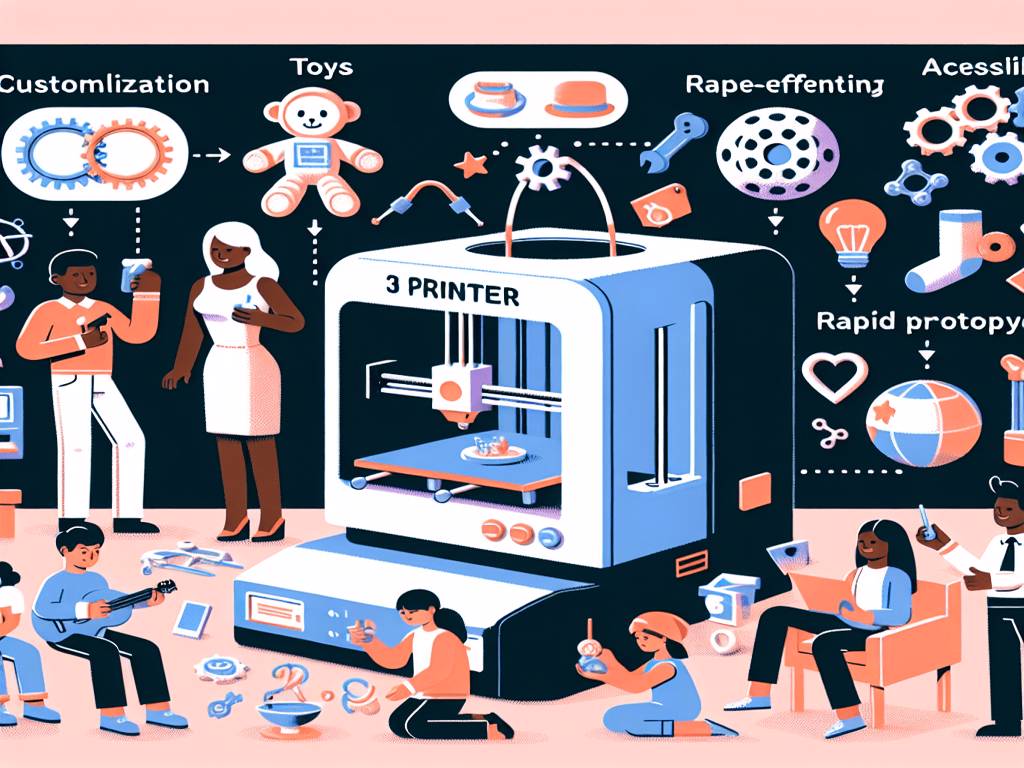
3D printing, also known as additive manufacturing, is ushering in a new era in the consumer goods industry. This technology is breathing new life into various consumer products, fueling innovation and creating exciting opportunities for the industry’s future. From custom furniture and bicycles to unique wearables and eyewear, 3D printing allows for unprecedented precision and customization.
Multiple Material Printing
One of the significant advantages of 3D printing is its ability to use multiple printer jets to lay down different materials simultaneously. Companies are utilizing this feature to develop conductive materials and methods of printing micro batteries and electronic circuits directly into or onto the surfaces of consumer electronic devices. This capability extends to various applications, including medical equipment, transportation assets, aerospace components, measurement devices, telecom infrastructure, etc.
Rapid Production and Cost Savings
3D printing technologies dramatically reduce time to market as 3-dimensional digital models can be printed immediately on commercial printers without complex set-up requirements. This rapid production capability and the cost savings associated with reduced material waste and less need for storage space make 3D printing a viable alternative to traditional manufacturing methods.
Customization and Consumer Participation
3D printing offers customization options for consumer goods that are unparalleled by other manufacturing methods. In some cases, it even allows the consumer to participate in creating the final object. For example, a sneaker can be created in the shoe industry after the wearer scans their feet. This level of customization is reshaping the consumer goods sector, allowing it to offer custom-made products that suit individual consumers’ needs and desires.
Durability and Intricate Designs
3D printing is not just about rapid production and customization. It also offers the ability to create products with intricate designs and high durability. As products designed for long-term usage traditionally require higher quality materials, intricate design, and longer production times to guarantee their endurance, 3D printing provides an exciting alternative. With the dawn of additive manufacturing, approaches to instilling durability have been excitingly overturned.
Key Advantages of 3D Printing for Consumer Products
Complex Design Capabilities
3D printing technology allows for the creation of more complex designs than traditional manufacturing processes. Traditional methods often come with design restrictions, but with 3D printing, these limitations no longer apply. This opens up a world of possibilities for intricate and innovative designs in consumer products, from eyewear to security solutions.
Speed and Efficiency
One of the main advantages of 3D printing is the speed at which parts can be produced. This technology can manufacture parts within hours, significantly speeding up prototyping. This efficiency allows each stage of the design and production process to be completed faster, making it a quicker and more cost-effective solution than traditional methods.
Print on Demand
3D printing offers the advantage of print-on-demand production. Unlike traditional manufacturing processes, this means there is no need for large spaces to stock inventory. This saves space and reduces costs, as there is no need to print in bulk unless required. This on-demand production also provides the opportunity for greater levels of personalization for finished or almost-finished goods.
Rapid Prototyping
3D printing allows for the quick and cost-effective creation of prototypes. This enables designers and engineers to iterate and test their ideas rapidly, reducing the development cycle and time to market for new products. This rapid prototyping capability is a significant advantage over traditional manufacturing techniques, which can be time-consuming and costly.
Customization and Personalization
3D printing makes it easy to create highly customized and personalized products. This technology makes it possible to service niche markets profitably, create low-production-run products that can command a higher price, and deliver a better profit margin. This level of customization is reshaping the consumer goods sector, allowing it to offer custom-made products that suit individual consumers’ needs and desires.
Cost Benefits
For small production runs, prototyping, small business, and educational use, 3D printing is vastly superior to other industrial methods in terms of cost. The technology reduces material waste and eliminates the need for storage space, making it a more economical choice for many businesses.
Innovation in Action: Real-World Applications of 3D Printing Across Consumer Industries
3D printing, or additive manufacturing, is making waves across various industries, driving innovation and transforming traditional manufacturing processes. Here are some real-world applications of 3D printing that demonstrate its transformative potential.
Consumer Electronics
In the consumer electronics industry, 3D printing is used to print micro batteries and electronic circuits directly onto the surfaces of devices. This innovative application extends to various smart devices, including medical equipment, transportation assets, aerospace components, and telecom infrastructure. Companies like Google are leveraging this technology to enhance their consumer electronics offerings.
Automotive Industry
The automotive industry is no stranger to 3D printing. Luxury automaker Porsche, for instance, has leveraged 3D printing and lattice design to introduce a new concept for sports car seating. This innovative application of 3D printing technology demonstrates its potential for customization and design flexibility in the automotive sector.
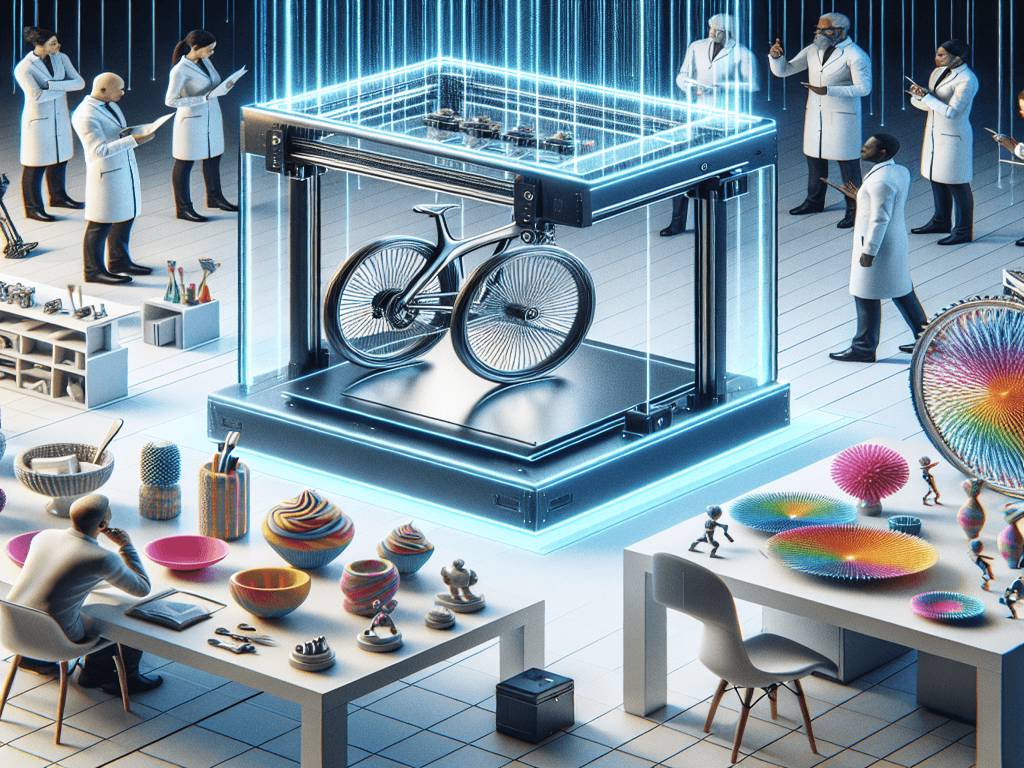
Replacement Parts Industry
The replacement parts industry is one of the most significant growth areas for 3D printing. 3D printing allows for parts to be printed on demand, eliminating the need for warehouse storage. Furthermore, a replacement can be designed and printed relatively quickly if a part is no longer manufactured. This application of 3D printing is causing a significant shift in the replacement parts industry.
Medical Industry
In the medical industry, 3D printing creates more durable and potentially longer-lasting metal joint implants. This application not only improves patient outcomes but also has the potential to save the medical industry significant costs.
Fashion and Apparel
In the fashion and apparel industry, 3D printing is being used to create 2D fabrics for clothing items such as hats, shoes, and gloves. This innovative application of 3D printing technology demonstrates its potential for customization and design flexibility in the fashion sector.
JuSheng: Transforming 3D Prototypes into Market-Ready Consumer Products
JuSheng is at the cutting edge of 3D printing technology, offering services ideally suited for creating rapid prototypes and intricate functional parts in large-scale production. Our facilities are equipped with the latest technologies and experienced operators, employing high-performance processes such as selective laser melting, selective laser sintering, stereolithography, and HP multijet fusion. These processes ensure precision, efficiency, and quality in every project.
As your one-stop shop for custom 3D prints, we provide a comprehensive selection of over 30 materials, including thermoplastics, thermosets, and metals. We also offer a wide range of post-processing techniques. If you need professional advice at any stage of the fabrication process, our team of experts is ready to guide you.
Contact us or upload your files for an instant quote. With JuSheng, you’re not just leveraging the latest in 3D printing technology; you’re partnering with a leader in the field.
Exploring Materials for 3D Printed Consumer Goods
Plastics: Plastics are the most commonly used materials in 3D printing, including ABS (Acrylonitrile Butadiene Styrene) and PLA (Polylactic Acid). These materials are easy to print with, cost-effective, and suitable for various applications, including toys, tools, and household items.
Resins: Resins are often used in Stereolithography (SLA) 3D printing. This material can produce highly detailed and complex objects, making it suitable for jewelry, dentistry, and model-making applications.
Metals: Metals such as titanium, aluminum, and stainless steel can be used in 3D printing, particularly in the aerospace, automotive, and medical industries. Metal printing requires more complex techniques like Powder Bed Fusion or Direct Metal Laser Sintering.
Ceramics: Ceramics can be used in 3D printing and are suitable for producing pottery, artworks, and complex industrial parts.
Biomaterials: In bioprinting, a variety of biomaterials can be used, including cells, collagen, and gels, for the fabrication of tissues and organs.
Concrete: In the construction industry, 3D printing technology can use materials like concrete to print houses and other large structures.
This is just a portion of the materials used in 3D printing, and it’s likely that as the technology advances, more new materials will be incorporated into 3D printing.
A Guide to 3D Printers for Consumer Product Creations
3D printing technology comes in various forms, each with unique characteristics, capabilities, and suitable applications. Here are some of the main types of 3D printers:
Fused Deposition Modeling (FDM): Fused Filament Fabrication (FFF) is one of the most widely available and inexpensive types of 3D printing technology. FDM printers construct 3D objects layer by layer, starting at the bottom and moving upwards by heating and extruding thermoplastic filament. This type of printer is excellent for beginners and is commonly used for prototyping and educational purposes.
Stereolithography (SLA): SLA is the original industrial 3D printing process. It uses a laser to cure liquid resin into hardened plastic. SLA printers excel at producing parts with high levels of detail, smooth surface finishes, and tight tolerances. They are widely used in the medical and entertainment industries and for creating various consumer products.
Selective Laser Sintering (SLS): SLS uses a laser to sinter powdered material, typically nylon, into a solid structure. The parts produced are robust and suitable for functional testing. They can support living hinges and snap-fits. SLS doesn’t require support structures, making it ideal for producing higher part quantities than other 3D printing processes.
Material Jetting (MJ): MJ printers have the broadest range of materials available and can easily print multi-material and multi-color parts. They deposit build material quickly, line-wise, allowing them to fabricate multiple objects in a single line without affecting build speed.
Multi Jet Fusion (MJF): MJF is a powder-based technology that uses a fusing agent and detailing agent applied in a thin layer across the powder bed. It’s then fused by heating elements into a solid layer. MJF printers can selectively color different parts of the print while also being able to place different material types into the same part.
Direct Metal Laser Sintering (DMLS): DMLS is a type of 3D printing technology that uses a laser to sinter powdered metal, forming a solid structure. This technology is often used in industries such as aerospace and automotive for its ability to produce substantial, durable parts.
Each of these 3D printing technologies has its strengths and limitations, and the choice between them depends on the project’s specific requirements, including the material, budget, desired quality, and purpose of the printed object.
Conclusion
3D printing is revolutionizing the consumer goods industry, breathing new life into various products and fueling new trends and innovation. The technology is creating exciting opportunities for the future of the consumer goods industry, from accelerating development cycles to enabling the production of customized goods.
The consumer goods industry has long recognized the benefits of 3D printing in product design and development, thanks to rapid prototyping. However, as 3D printing matures and more materials become available, the industry opens up to the new opportunities the technology offers for direct manufacturing.
Companies across the consumer goods sector are increasingly adopting 3D printing to provide more customer-centric services and products in a cost-effective manner. The technology is being used to fabricate various products, from computer hardware and custom shoe insoles to audio equipment components and furniture.
3D printing offers customization options for consumer goods, allowing consumers to participate in creating the final product. For example, a sneaker can be made in the shoe industry after the wearer scans their feet. This level of customization is more efficient and practical and enhances the aesthetic appeal of the products.
Moreover, 3D printing is a sustainable manufacturing process. It avoids technology and process-related material waste and overproduction and can use raw materials from renewable sources. This demand-driven production means digitally configured products can be made precisely when needed, even at the point of sale.
Pingback: What Is The Difference Between 3D Printing PLA And ABS Filament? - JUSHENG
Pingback: PLA vs. PLA Plus: Which Filament Is Better? - JUSHENG
Pingback: PLA vs. PETG: The Ultimate Filament Guide - JUSHENG
Pingback: The Hidden Difference Between PVA And HIPS Is Misunderstood By 99% Of People! - JUSHENG
Pingback: Classification Of Filament Used In 3D Printers - JUSHENG